戦略的工場経営ブログ工場でビックデータを活かす2つの着眼点
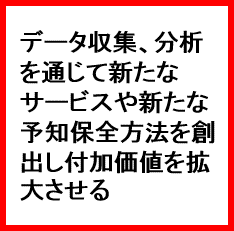
データ収集、分析を通じて新たなサービスや新たな予知保全方法を生み出す、と言う話です。 自社製品に関連した新たなサービスや 自社設備の新たな保全方法のアイデアがありますか? ウチの製品がお客さんのところで使われているトコロを実際に見る機会は少ないなぁ。 現場の設備はベテランに修理させているので、もしかしたら勘所を押さえているかもしれない。 新たなサービスや設備保全方法を考えるにはどうすればいいだろう? 自社製品や自社工場の製造ラインを知り尽くすことです。 顧客先で自社製品が どのように使われているか、 また現場ベテランがどのように対応しているのか調査します。
1.インダストリー4.0とインダストリアル・インターネット
ドイツのインダストリー4.0と類似した概念があります。 アメリカのインダストリアル・インターネットという概念です。 ドイツのインダストリー4.0が発表されたのが2011年です。 アメリカのインダストリアル・インターネットは2012年に提唱されました。 インダストリー4.0の方が若干先輩です。 インダストリアル・インターネットを提唱したのはGeneral Electric(GE)です。 この概念を世界に広げる取り組みを しているのがインダストリアル・インターネット・コンソーシアムです。 GE社などのアメリカ企業を中心に設立された民間企業主導の団体です。 インターネットを産業に利用しようとする 各種プロジェクトには、多くの共通点があります。 ビジネスモデルの構築、基礎技術の開発などです。 それならば、バラバラでやるよりは一緒に取り組んだ方がヨイ、という考えに至りました。 GEが提唱する インダストリアル・インタ―ネットは ドイツのインダストリー4.0よりは、概念に具体性があって理解し易いです。 GEが掲げる全体像は次のようなモノです。 1)センサーを埋め込んだ各種機器からネット経由でビッグデータを採取する 2)ビッグデータを蓄積する 3)ビックデータを分析し、洞察を導く 4)具体的な行動へ移す ビックデータで分析、洞察したことを、 現場ですぐに使える「アクショナブル・インフォメーション」に加工するところがポイントです。 具現化できそうな事例がいくつかあります。 1)航空機エンジン 商用航空機は全世界で2万機、 ジェットエンジンは4万台程度存在しており、今後も増えるようです。 離発着時の遅延時間の遅延やトラブルの41%がメカニカルエラーで占められています。 これによる航空業界の負担コストは一日あたり4500万ドル!!です。 その一方で、航空機のエンジンは大量のデータを生成しています。 しかし、実際に利用されているのはごく一部に過ぎません。 そこで、このデータをリアルタイムに収集・分析するのです。 負担コスト削減を実現したい航空会社へ有益なサービスを提供できます。 早い段階でエンジンの不具合を見つけ、 メカニカルエラーを予知できれば、トラブルを防止でき、コスト負担が減ります。 また、発電システムでも同様な事例があります。 稼働中のタービンの動きをネット経由でリアルタイムに監視します。 故障の予兆を見極めるトラブル防止サービスです。 ビッグデータ分析で故障を先回りし、 オペレーターが対処に当たることを目指します。 日本GEの田中豊人GEコーポレート専務執行役員は、 「定期保守が不要になる日が来るかもしれない」と語っています。 コトが起きてから動くのではなく、トラブルを未然に防ぐわけです。 儲かる工場経営でもこうした仕組みを目指します。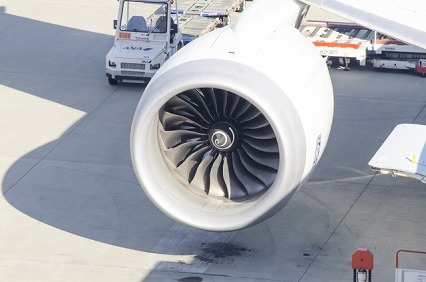
2.自動車部品の製造現場を管理していた頃の話
自動車部品の製造現場を管理していた頃の話です。 その現場では特殊鋼製の部品を扱っていました。 手のひらサイズの小さな部品でしたが、毎月数十万個を納入していました。 その部品は顧客先でさらに加工されます。 油分が付着した状態で加工させると、顧客先で不具合が発生します。 したがって、場内では防錆用の油を塗布できませんでした。 全数検査して、製品梱包してから約2日後に納入していました。 その程度の在庫期間なら錆が発生するリスクは低かったのです。 しかしながら、出荷までの1~2日間でサビが発生するケースも稀にありました。 そのような場合に備え、出荷前に抜き取りの外観再検査も行っていました。 ただ、抜き取り検査の工数も無視できませんでした。 何らかの根拠をもって抜き取り頻度を減らしたいとの要望が出てきました。 もしも、サビが発生しやすい状況を把握できれば、効率的な再検査が可能になります。 そこで、データの収集を計画しました。 サビが発生するのは現場の気温と湿度が関係していると仮定をしました。 両者がある数値以上になったら錆びが発生するリスクが高まる。 そこで、データロガーで気温と湿度、 そして、その時のサビ発生具合を調査し続けることにしました。 横軸に気温、縦軸に湿度のマトリックスにサビの発生具合の分布を記します。 気温-湿度-サビ発生状況の相関図が手に入ります。 実績を積んでいけば、気温と湿度の組み合わせからサビのリスクを判断できます。 当時は手作業で集計をしていました。 ビックデータと言うほどのデータ量はなかったわけですが。 画像認識装置なども活用し、 ネットワークでデータ収集し、 データを蓄積し、 分析を進めれば、まさに、(セミ)インダストリアル・インタ―ネットです。 データの収集・分析により、モノづくり現場で発生している現象を 解明することが可能になります。3.中小企業のモノづくり工場でIOTを活かす
インダストリー4.0よりも インダストリアル・インターネットの方が、その概念に具体性があって理解し易やすいです。 データを収集→蓄積→分析し、 対策・行動につなげる。 カイゼンでの問題解決手法です。 情報通信技術(ICT)の進歩で 驚くほどのデータ量を安価に処理できる時代がきました。 クラウドソーシングのサービスもますます進化します。 手元にデータベースが無くても、必要に応じて大容量のデータベースを安価に活用できるのです。 こうした技術を活用して、高付加価値化を図れないか? わたしたち中小ものづくり企業の課題です。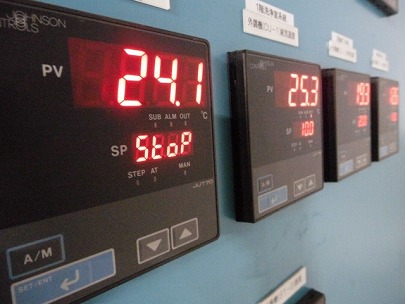