戦略的工場経営ブログ変化に着目して品質管理の3つの見える化を実践する
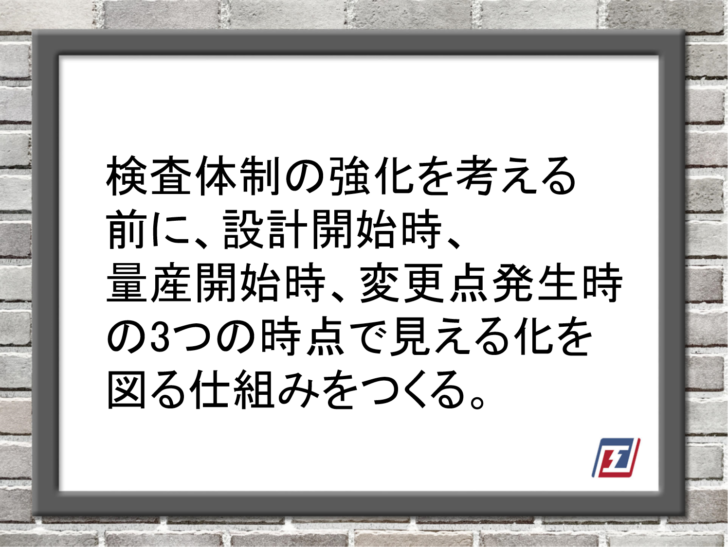
検査体制の強化を考える前にやるべきことがある。
設計開始時、量産開始時、変更点発生時。
3つの時点での見える化を実践する、という話です。
品質管理する仕組み/体制は機能していますか?
生産活動を優先しがちで、
検査を強化するためのお金も人も足りないなぁ。
品質が重要であることは分かっているけれど・・。
専任の検査担当者を置きたいけど、
作業との兼務体制にならざるを得ない・・。
余力がない中、工場の品質管理を強化するイイ方法はないのだろうか?
製品開発から生産までの業務フローのなかで「変化」に着目した仕組みを考えます。
具体的には、デザインレビューであり、初期流動管理であり、工程変更管理です。
1.日本製品の品質レベルが低下している
トヨタ自動車では2009年~2010年に、
大規模なリコールを実施しました。
モノ作りに携わる人ならば、
改めて”品質”を強く意識するきっかけになった出来事でした。
運転中に「意図せぬ急加速」が起きるとされました。
アクセルペダルに加えて、電子制御装置にも異常があるのではないかとの指摘を受けました。
豊田章男社長がアメリカの議会に公聴会に呼ばれるほど深刻な事態に至ったリコールです。
事態が収束に向かいつつあるなか、
豊田章男社長はアメリカのトヨタ関係者を前にして再起への決意を語っていました。
関係者の誠意ある対応への感謝を涙ながらに語っていた姿が印象的でした。
(あの雰囲気は、社長が創業者豊田家であったからこそ出せたとも感じました。
サラリーマン社長で心に響く言葉を語れる方はどれだけいるだろうか?)
品質は顧客と構築する信頼関係の土台、前提条件です。
顧客にとってはあってあたりまえ、メーカーにとってはトラブルがなくてあたりまえ。
継続的で地道な取り組みが求められるのが品質です。
その品質レベルが低下していると感じている技術者の割合は増えています。
下記は、技術者に日本製品のレベルを聞いた結果です。
回答数は、2010年で1361名、2015年で439名です。
(出典:日経ものづくり 2015年7月号)
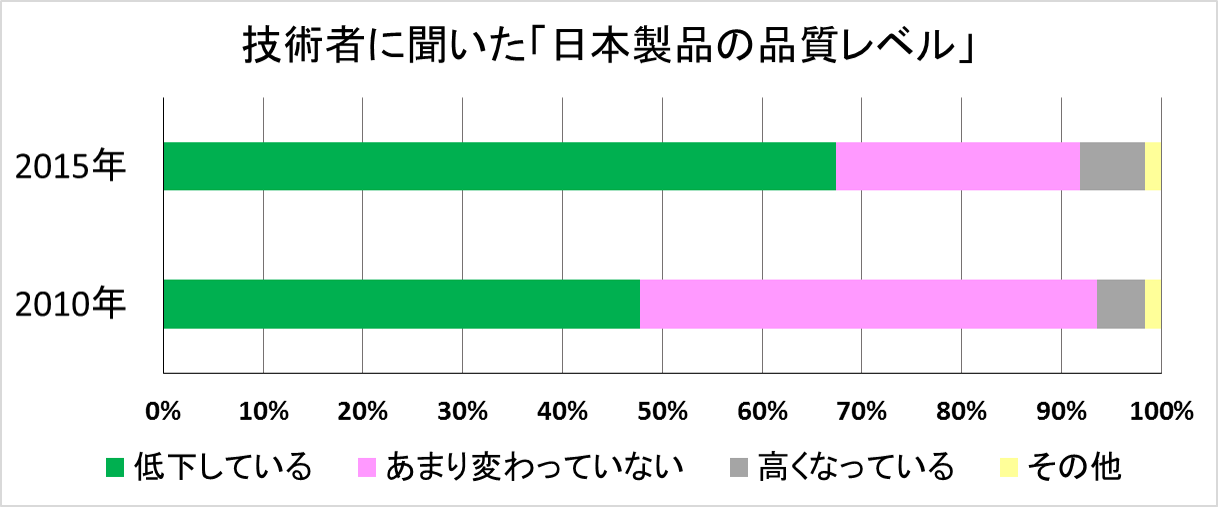
品質が低下していると感じている技術者が増えています。
2010年対比で2015年は20%増え70%に達しています。
貴社の製品ではどうですか?
以前と比較して品質への感度は低下していませんか?
先のトヨタの事例だけでなく、その後も、
2013年から2014年にかけてホンダでリコールが頻発しました。
他に、
タカタのエアバック、
東洋ゴム工業の建築用免振ゴム問題、
旭化成建材の杭打ち工事問題、
等、規模の大きな品質トラブル事例の枚挙に暇がないです。
2.品質低下を助長する、現場を取り巻く環境変化
メーカーでの品質管理を難しくしている経営環境の変化には5つのポイントがある。
「日経ものづくり」では、こう指摘しています。
(出典:日経ものづくり 2015年7月号)
・工場の現場力低下
・電子化による製品の複雑化
・進むグローバル化
・流通企業のメーカー化
・絶え間ないコスト削減圧力
貴社の工場に当てはまる項目はありますか?
特に「工場の現場力低下」は気になります。
自動車メーカーでは上記の5つの問題、
程度の差こそあれ、全てに直面しています。
これらの取り組みは中小製造業でも参考になります。
トヨタは、2015年に
「TNGA(TOYOTA NEW GLOBAL ARCHITECURE)」
を発表しました。
部品、ユニットの共通化を進め、開発の効率化を進めることが狙いです。
トヨタの新しいクルマ作りの方針です。
搭載するユニットや配置、ドライビングポジションなどを設計思想に定めています。
この新プラットフォームは
2015年に販売された新型プリウスαに搭載されました。
トヨタ自動車技監の佐々木眞一氏が以下のように解説しています。
「TNAGの品質管理におけるメリットは、
的が絞れる、変化点がクリアに見える、
ということです。
何を変えて、
何を変えないのかがはっきりする。」
(出典:日経ものづくり 2015年7月号)
つまり、トヨタでは、
今後設計される新車で変えてはいけないことをはっきりさせています。
ですから、これからは、”変わった部分”に重点を置いて品質管理をやればいいわけです。
的を絞った品質管理を可能にしています。
3.現場では「変化」に注目した仕組みを作る
トヨタの「変わるところと変わらないところ」という視点に注目です。
我々、中小のモノづくり現場へも活用ができます。
中小現場でも専任の検査員を置いて、
客観的な立場で、検査業務を実施するのが理想です。
しかし、現実には様々な制約条件のもと、
作業と検査を兼務する体制を継続しなければならないことも多いです。
そこで、新たな仕組みを加えて、
作業と検査を兼務する体制でも品質への感度を高い状態を維持できるようにします。
製品開発から生産までの業務フローのなかで「、変化」に着目した仕組みをつくります。
注目するのは、次の3つの時点です。
設計開始時、量産開始時、変更点発生時。
品質に関するコストは次の4種類あります。
1)予防原価 製品の規格に一致しない製品の生産を予防するコスト
2)評価原価 製品の規格に一致しない製品を発見するためのコスト
3)内部失敗コスト 工場内で発生する部品、製品の仕損、補修のためのコスト
4)外部失敗コスト 欠陥部品の販売によって発生するコスト
1)から4)へ進むに従って、コストがかかります。
問題が起こってしまってから現状復帰させるためのコスト。
問題を発生させないための仕組みづくりにかかるコスト。
前者は後者よりも大きいと言われています。
さらに費用それ自体もさることながら、無形財産のロスによるダメージも大きいです。
信用の失墜、特に現場モチベーションの低下、不具合品の外部流出による企業イメージの低下等々。
失った無形財産を復活させるコストは無限大です。
ですから、問題が起きる前に手を打ちます。
設計開始時、量産開始時、変更点発生時にチェックする仕組みを構築します。
3-1 設計開始時のデザインレビュー
現場には長年のモノづくりで蓄積された貴重なノウハウがあります。
どのような仕様の場合にトラブルが発生しやすいか、どのような形状なら造り易いか。
こうした情報を新製品設計の段階で反映させてしまいます。
過去を振り返って、細かい事項でもなんでも、現場の情報を吸い上げるのです。
対応可能な新たな項目を製品の仕様に加え、従来仕様の変更を実施します。
こうしたデザインレビューこそが品質管理の出発点です。
自動車工場部品を製造していた工場で勤務していた時の話です。
新製品開発時には必ず、デザインレビューを実施していました。
この仕組みによって、事前に不具合を潰すことが可能でした。
どれだけ量産の垂直立ち上げに貢献したかしれません。
量産立ち上がり時の試行錯誤が許されない製品も、まれにありました。
売れ行き好調という車種の製品の場合などです。
こうした製品で、この仕組みはとても役に立ちました。
デザインレビューは全工程の現場責任者が集まって意見交換する場です。
ですから、一体感を醸成するのにも役に立ちます。
3-2 生産開始時の初期流動管理
生産が立ち上がってから所定の期間は、
”特別に”手間かけて品質実績を把握する努力をする、ということです。
新製品、新部品の量産を始めるにあたって、
現場全体に品質を意識させる仕組みはありますか?
あるいは、新しい製品でも「なんとなく」量産が開始してしまいますか?
生産の数量や頻度にもよりますが、
少なくとも2~3ロット分の生産指示に対応して、品質を特別に注視します。
その生産の品質状況を「あえて」詳細に監視する体制をつくるのです。
各工程上の品質管理上のキモを、事前に、明確にしておきます。
そして、各工程では、あえて手間をかけて品質を確認する。
得られた結果から、今後も継続して検査すべし、という項目を見つけ出します。
製品仕様に起因する不具合は概ね全てこの初期流動管理期間で抽出されます。
品質見える化によって、引き続きやるべきことが見えてきます。
3-3 変更点発生時の工程変更管理
これは、今からでもすぐにできます。
やっていそうで、意外とやられていない管理です。
長い間、量産していると様々な理由で仕様や生産設備などが変更されることがあります。
変化の情報を共有し、この変化の影響で品質が悪化しないか確認します。
そして、変化に対応した品質の確認を実施して結果を整理するのです。
良かれと考えて現場が実施したことが、他の関係者に伝わっていなかったため、
それが原因でトラブルが発生することが往々にしてあります。
これまでの経験では、デザインレビューと初期流動管理は、ある程度の確率で現場へ定着できます。
一方、この工程変更管理は、
よほど管理者の意識が高くないと定着させることは、難しです。
ただし、とても役に立つ仕組みです。
モノづくり現場は日々、細かい改善活動を積み重ねています。
現場の細かい対応の履歴をしっかり残すことで、気づきがあるからです。
現場管理者が自工程の状況を精度よく把握するために威力を発揮します。
関係者の”記憶”に頼って現場管理をするには、現在、いろいろなことが複雑になりすぎています。
本来は現場の検査体制の構築を考えたいです。
ただし、多くの制約上条件があるのも現実です。
ですから、まずは3つの仕組み
(デザインレビュー、初期流動管理、工程変更管理)で品質への感度を上げます。
まとめ。
製品開発から生産までの業務フローのなかで「変化」に着目した仕組みを考える。
具体的には、デザインレビューであり、初期流動管理であり、工程変更管理。
モノづくりの現場で品質管理を強化する時は、
検査体制の強化を考える前に、
設計開始時、量産開始時、変更点発生時の
3つの時点での見える化を実践する、という話です。