戦略的工場経営ブログボトルネック工程を解消して、モノの流れを改善する
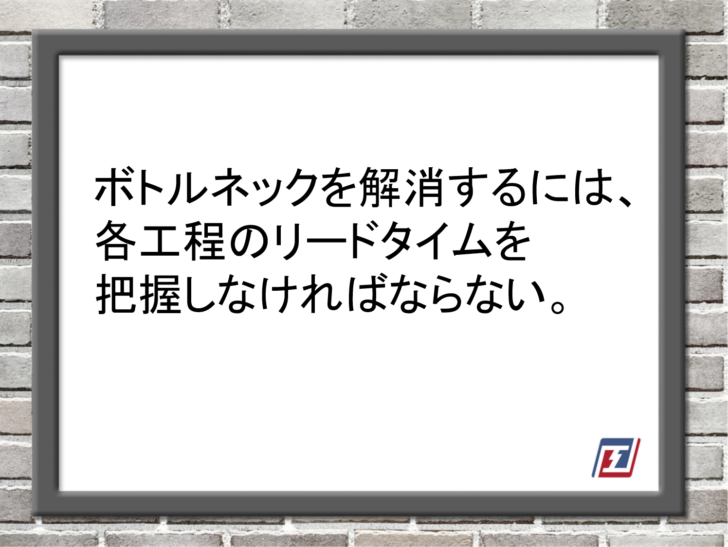
貴社ではボトルネック工程を把握して、適切な対応をしていますか?
1.生産管理で”流れ”をチェックする
儲かる工場経営は、「儲かる生産管理」の設計から始まります。
生産管理体制の整備抜きに、改善活動やその他現場活動をやっても効果を最大化できません。
標準が整備されていない現場で、どんな活動を展開しても活動自体が定着しないからです。
比べる基準がなければ、仕事は成立しません。
また、全体最適化の視点を持つことができず、部分最適化に留まり、効果も限定的です。
セミナーやご指導で、弊社が「生産管理」の重要性を繰り返し申し上げているのは、そうした理由からです。
貴社では、生産管理体制が、整備されていますか?
そして、生産管理で、チェックするのは、”流れ”です。
弊社では、3つの流れに着目して、現場をチェックします。
・モノ
・お金
・情報
3つの視点で、現場の”流れ”を見るのです。
流れが滞っているところを探します。
2.ボトルネック工程
流れが滞っているところとは、「ボトルネック」のことです。
各工程の生産能力評価や現場観察を通じて、工場全体の生産能力を制約する「ボトルネック」を見つけます。
他の工程で、どんなに生産性を高めても、結局は、ボトルネック工程が全体の生産能力を決定するのです。
ですから、ボトルネック工程の解消が、”流れ”の滞りを解消することになり、全体の生産性を高めます。
ボトルネック工程を見つけるのに必要な生産能力を評価することが必要です。
それが、各工程の生産リードタイム(タクトタイム)です。
各工程の生産リードタイムを、3つの視点で評価します。
①差立て(作業手配)して作業に着手するまでの時間
②準備段取り時間
③主体作業時間(正味時間+余裕時間)
①+②+③の総時間で、各工程の生産リードタイムを評価するのです。
ポイントは、工程間の①、②、③の定義を同じにすることです。
唯一絶対の定義はありません。
現場独自に決定する定義となります。
定義の際には、個別生産、ロット生産、連続生産の生産形態による差異を考えることです。
こうして、適切な定義を定め、各工程の生産リードタイムを評価します。
そして、生産リードタイムが最も長い工程が、ボトルネック工程です。
原則、他の工程は、ボトルネック工程の生産リードタイムに合わせて生産します。
工程間の仕掛品を、最小化するためです。
そして、ボトルネック工程の稼働を最大化します。
ボトルネック工程は、絶対に止めてはならないのです。
ボトルネック工程の前にはある程度の仕掛在庫を保持しておくことも必要となります。
そして、ボトルネック工程と同期化して、他工程を稼働させるのです。
モノの停滞を最小化します。
モノの停滞を最小化するということは、言い換えると、お金の停滞を最小化することです。
キャッシュフローの視点からも効果は評価できます。
したがって、ボトルネックを見つけた後は、下記のように生産管理をすることが望ましいのです。
1)生産工程全体はボトルネック工程の生産リードタイムに合わせる
2)ボトルネック工程の稼働を最大化するため直前に必要な仕掛在庫を設定する
3)各工程はボトルネック工程と同期化させる
3.主体作業や準備段取り作業以外で注目すること
モノの停滞を最小化することは、キャッシュフローの改善につながります。
生産管理上の課題は、ボトルネックの解消です。
具体的には、①+②+③総時間が最長になる工程において、①、②、③を短縮することです。
ここで、着目したいことがあります。
それは、①です。
意外と①で、時間を要している工程はないか?ということです。
生産計画を立案し、差立て(作業手配)を現場へ提示するけれども・・・。
作業着手までに、時間がかかっている工程はありませんか?
板金製品の生産管理を担当していたときの話です。
最上流工程となる材料切断工程の生産リードタイムが、決定しにくい状況にありました。
一方、主要工程であるプレスや曲げ、切削加工などは、生産リードタイムを設定できていました。
なぜ、最上流工程で、リードタイムが決定しにくいのか?
下記のような事情があったのです。
2つの工場で使用される材料を、1か所の切断工程で賄っていました。
加えて、外注先へ支給される切断品も、そこの工程が担当していました。
そして、その現場では、生産管理体制が未整備状態だったのです。
現場担当者や生産管理担当者の属人的な調整作業によって、工程が決まっていました。
切断依頼情報が、一元管理されていないため、全体最適化が見通せない状況でした。
その結果、生産リードタイムの設定は、現場の事情で大きく左右され、確定できなかったのです。
切断工程の現場担当者は、最適な工程を組もうと頑張っていました。
現場作業をしながら、届いた切断依頼情報を元に、工夫をしていたのです。
しかし、情報が一元化されていないので、現場担当者も全体を見通すことができませんでした。
本来であったなら、
1.切断情報の一元管理と工程管理のルール化
2.月間計画と週間計画の共有化
これらの取り組みで、
最上流工程となる材料切断工程の生産リードタイムの見える化と短縮化が図れた思われます。
現場担当者もストレスを感じないで、最適な工程を組むことができたでことでしょう。
心残りとなった未達の課題です。
ボトルネック工程の解消では、各工程の生産リードタイムの把握と短縮化がポイントです。
そして、生産リードタイム短縮化では、主体作業や準備段取り作業以外の要因にも着目します。
①差立て(作業手配)して作業に着手するまでの時間
①の時間に、無駄がないかチェックして下さい。
ボトルネック工程評価の仕組みをつくりませんか?