戦略的工場経営ブログ移動が伴う工程分析はフローダイヤグラムでムダ探し
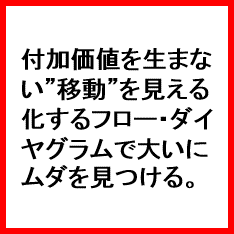
移動が伴う動きの分析にはフロー・ダイヤグラムを活用して、工程分析の精度 上げる。付加価値を生まない”移動”を見える化するフロー・ダイヤグラムで 大いにムダを見つける、という話です。
1.「停滞」や「手待ち」は止まっているので認識しやすい
工場オペレーションで目指すのはイイ流れの工場です。 QCDのQもCもDも、全て、イイ流れを作れば望ましい姿へ進みます。 工場の役割は、現場で付加した価値をお金へ滞りなく変換することにある、と いうことに思い至れば、自然と気が付くのではないでしょうか。 ですから現場リーダーや各工程のキーパーソンは現場の”流れ”を意識するこ とで、いろいろなことが見えてくるはずです。 ワークの流れ、情報の流れ、人の流れ、・・・・。 自社工場に当てはめて、自分の職場における、望ましい”流れ”を常にイメー ジしておくことが欠かせません。 現状と望ましい姿とのギャップを認識するための基準を持つためです。 カイゼンとはチームオペレーションを最大限に機能させるべき現場の自主的な 活動です。 チーム力を120%発揮させるために、まずは、チーム全員で望ましい姿を共 有します。 オペレーション・プロセス・チャートは製品やプロセスの”本質”を見える化 するための手法であり、”物”に注目し「加工」と「検査」に絞った流れを把 握します。 (工程分析で製造プロセスの本質を見える化する) このオペレーション・プロセス・チャートでは、”本質”を共有することが重要 です。 その後、全ての要素工程を洗い出すフロー・プロセス・チャートで全体を分析 します。 物の「停滞」と人の「手待ち」に注目することで工場のムダを認識できます。 (工程分析で物の「停滞」は親の仇のごとくヤッツケロ) あらゆる面で、現場にイイ流れを作りたいわけです。 イイ流れに対して止まっていたらヨクナイコトというのは分かりやすいです。 物が「停滞」することや人が「手待ち」していることがヨクナイコトであり、 そして「停滞」や「手待ち」は止まっているので認識はしやすいです。 ただし、これらを抜本的に解決するには、時間がかかるかもしれません。 カイゼンすべき問題点と認識しやすいけれども、対応策は容易ではないケース は多いかもしれません。 すぐに手は打てなくても、将来的には必ず、カイゼンのテーマとして取り上げ たい事項です。 全ては工場にイイ流れをつくるためです。2.意外と気が付かない「ムダ」
生産管理の解説本でしばしば語られますが「動く」と「働く」は違います。 「動く」イコール「働く」ではないので、忙しそうに動き回って汗をかいて いるからと言って、必ずしもイイ仕事をしているわけではない・・・・・。 ただ、目に触れる分、一生懸命になって働いているように評価される・・。 仕事の評価が、内容よりも”時間”でなされる雰囲気の現場では、特にその ように、とらえられる傾向が強いかもしれません。 現場で唯一、付加価値を生み出すのは「加工」のみ。 それ以外は、どれだけ汗をかこうが、時間をかけようが付加価値、つまりお金 は生み出さない。 現場では、しっかり理解しておく必要があります。 そして、イイ流れは作りたいのですが、無駄な流れや動きは排除したいです。 ”一定位置”での動きが「動く」なのか「働く」なのかは、全ての要素工程 を洗い出すフロー・プロセス・チャートで判断できます。 「人」を対象にすれば、動作の本質を知ることができるからです。 ただし、動作に”移動”を伴う場合、フロー・プロセス・チャートでは見え にくい要因があります。 それは、距離感。 チャートへ距離を数値で記入する手がありますが、いま一つ、感覚的につかみ難い。 そこで活用したいのが、フロー・ダイヤグラムです。フロー・ダイヤグラムとは、建物、機械設備、作業域などのレイアウト図に物 または人の移動経路を線図に表し、プロセスを分析するための手法である。物の移動や人の移動を、そのものずばり記録し分析します。 ポイントは”一定位置”での動きではなく、”移動”をともなう動きに着目す ることであり、この”移動”を分析することです。 例えば、運搬作業はそれ自体で詳細に分析されることもあります。 そうした詳細分析の前に、対象物の”移動”を伴う動きを分析して全体を把握する。 ”移動”を伴う詳細分析の前に、事前に、鳥の目で”移動”全体を見える化する のがフロー・ダイヤグラムの目的です。 ・物に着目したフロー・ダイヤグラム ・人に着目したフロー・ダイヤグラム それぞれありますが、機能別レイアウトが大部分である中小現場であるならば ”人”に着目すれば全てを語ることになります。 物がかってに移動することはないですから。 製品別レイアウトなら、コンベヤやその他の手段で”物”を流動させますが、 こうしたレイアウトで、ムダがあるという例はあまりないでしょう。 そのあたりは、事前検討でやられているからです。 それでも、あえてコンベアを撤去し、工程と工程の間を詰めたり、あるいはラ イン形式からU字ラインや一人生産方式に移行する取り組みもありますが、今 は、多くの中小現場がそうである機能別レイアトを想定します。 機能別レイアウトでの動きの主役は人です。 機能別に並べられた設備や装置へ、”人”が必要なものを運ぶのが基本ですから、 人やフォークリフトが動かないとワークも移動しません。 こうした、必要悪的な”動き”があることを前提にして、ムダな動きを探すのです。 「動き」があると、一見するすると一生懸命に「働いて」いるように見えるこ とに留意します。 「動き」があると、それがムダであっても気が付きにくいです。 その動きが常態化されているならばなおさらです。 工程分析ではフロー・ダイヤグラムを補完的に活用することでムダを把握しや すくします。 「動き」に惑わされず、ムダを抽出します。(出典:IEの基礎 藤田彰久)
3.加工組み立て工場の現場で経験したこと
加工組み立て工場の現場でカイゼンを経験したことがあります。 そこの現場には”運搬専門”の担当者がいました。 その担当者の業務を対象にしました。 動くことが仕事(?)のような役割ですから分析する価値がありました。 決まったプロセスがない業務の場合、履歴を追うという目的でフロー・ダイヤ グラムで動きを整理します。 ダイヤグラムの軌跡を眺めると、 ・特定の場所での往復移動 ・散発してみられる長距離移動 ダイヤグラムに描くと、上記が一目で”感覚的”に理解できます。 ”距離感”ということでは、運搬作業で工場内をフォークリフトで1日あたり でのべ3~4km走行している実績が明確になり、”それはあまりに走りすぎ だ”ということで、物流を見直そうという機運が高まった自動車部品製造現場 もありました。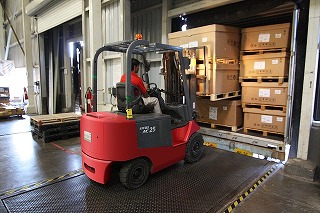