戦略的工場経営ブログ生産性と生産リードタイム、どちらを気にしますか?
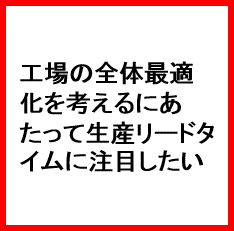
工場の全体最適化では生産リードタイムに注目したい、という話です。 付加価値創出と関連のある指標は何だろうか? 儲かる工場経営で持つべきイメージのひとつに「流れ」があります。 製品が滞りなく流れていくイメージです。 投入した資金を一日でも早く、現金で回収したいからです。
1.実現させたい将来の姿を描くのに問題を認識する
現場で進捗管理をしているといろいろな問題に直面します。 現場が環境の変化に追随できていないからです。 諸問題は現場の弱いところ指摘しています。 こうした問題はカイゼンのきっかけになります。 ・進捗管理で計画対比の遅れを認識する(=問題を認識する)。 ・対策管理表で対策のPDCAを廻す。 生産計画対比の遅れから問題点を認識し、対策のPDCAを継続的に廻します。 この仕組みが構築されている現場は存続し成長できます。 仕組みで情報的経営資源も蓄積しているからです。 情報的経営資源は存続と成長に欠かせないイノベーションの土台となります。 (進捗管理で顕在化した問題点が意味することとは) 問題が認識されたら、まずは暫定策を打ちます。 どんな手でもいいから出血は即、止めなければなりません。 そして、問題を課題に変換するのです。 抜本的に問題を解決するためです。 イノベーションを生む機会とします。 現場の問題を経営課題へ変換する仕事は経営者にしかできません。 目指すべき状態は経営者にしか描けないからです。2.生産性と生産リードタイムはしっかり切り分けて考える
進捗管理の問題点は”遅れ”で認識されます。 各工程内での発生したいろいろなトラブルが原因です。 ・段取りに時間がかかってしまった。 ・必要な材料が届いていなかった。 ・加工を失敗して、造りなおした。 ・作業者が急に休んで、人手が足りなかった。 等々。 トラブルが発生すると、生産性が低下します。 生産リードタイムが伸びて、納期に遅れが出ます。 ですから、現場は早速、暫定策を講じます。 ・段取り時間を管理しよう。 ・資材の在庫を管理しよう。 ・加工作業時のチェックポイントを新たに設けよう。 ・突発の休みでも対応できる人員配置を新たに考えよう。 まずは、出血をとめなければなりません。 当然の対応です。 ただし、一時的に出血を止めても必ずしも問題の根本的な解決になるとは限らない。 将来の目指すべき状態を設定して、問題を課題へ変換する必要があります。 もう一歩踏み込んで現場の弱みを把握するのです。 そこで、生産性とリードタイムに着目します。 そして、どちらを重視するか判断するのです。 将来の目指すべき状態のためには、どちらが効果的な指標になるでしょうか? ここである生産ラインを考えます。 工程1と工程2の2つの工程で構成されている生産ラインです。 ・この生産ラインは製品を60個単位でロット生産しています。 ・工程1では作業者が5人で2日掛かっています。 ・工程2では作業者が10人で1日掛かっています。 ・生産能力に制約があるため、工程1と工程2の間で仕掛品が1日滞留します。 この状況が標準です。 さて、今、工程2でトラブルが発生したと仮定します。 その結果、生産性が低下し、生産リードタイムが伸びました。 これらの状況を下表にまとめます。工数あるいは日数 | 生産指標 | ||||
工程1 | 仕掛 | 工程2 | 生産性 | 生産リードタイム | |
標準 | 5人×2日 | 1日 | 10人×1日 | 3個/人・日 | 4日 |
トラブルA | 5人×2日 | 1日 | 10人×2日 | 2個/人・日 | 5日 |
トラブルB | 5人×2日 | 2日 | 10人×1日 | 3個/人・日 | 5日 |