戦略的工場経営ブログ品質不正を未然に防ぐ唯一の方法
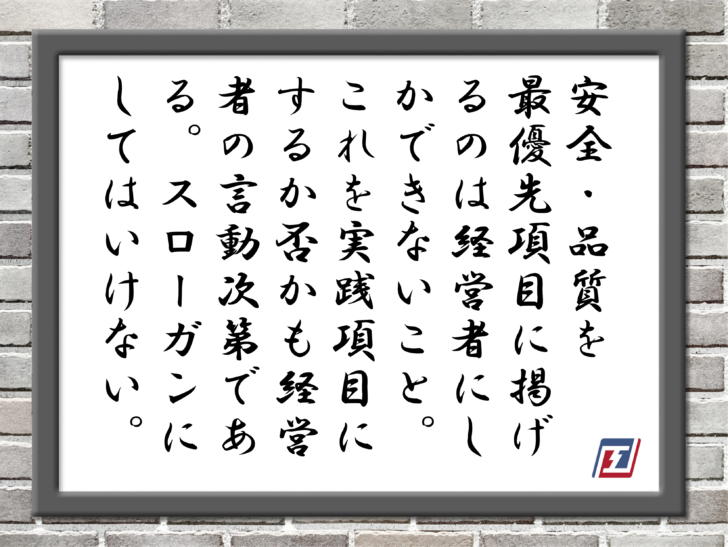
1.大手製造企業の品質不正問題
日経ものづくり2021年7月号では「日本の品質再定義」を特集しました。特集の中で2016年4月から2021年4月時点での品質問題事例を列記しています。
この5年間に深刻な案件だけでも40余りの事例があるようです。同記事で挙げた事例を下記に示します。(出典:日経ものづくり2021年7月号)
2016年
4月 三菱自動車 軽自動車の燃費試験不正を公表
5月 スズキ 燃費試験不正を公表
6月 神鋼鋼線ステンレス ばね用ステンレス鋼線の強度試験データで改ざんが発覚
2017年
2月 三菱電線工業 シール材の寸法と材料物性の測定値で改ざんが発覚
6月 タカタ 欠陥エアバックの異常破裂問題で経営破綻
8月 神戸製鋼 アルミ・銅、鉄鋼製品などで検査データの改ざんが発覚
9月 日産自動車 完成検査の不正(無資格検査員)が発覚
10月 SUBARU 完成検査の不正(無資格検査員)が発覚
10月 三菱伸銅 黄銅条や銅条製品の検査データを改ざん
11月 東レハイブリットコード 自動車用補強材の検査データの改ざんを公表
11月 シチズン電子 LED部品などで製造拠点の偽造が発覚
12月 SUBARU 燃費・排出ガス検査不正が発覚
2018年
1月 トーカン ゴム製品で品質データ偽造が発覚
2月 丸善石油化学 樹脂などの品質データねつ造と試験不正を発表
2月 三菱アルミニウム、立花金属工業、ダイヤメット 品質データ偽造を公表
2月 宇部興産 低密度ポリエチレン製品で品質データねつ造を公表
6月 三菱マテリアル 銅スラグ骨材工場がJIS認証の取り消し処分
7月 日産自動車 燃費・排出ガス検査不正を公表
8月 スズキ、マツダ、ヤマハ発動機 燃費・排出ガス検査不正を公表
9月 日産自動車 精密車両測定の検査不正を公表
9月 SUBARU ブレーキや舵角などの検査不正を報告
10月 日立化成 エポキシ樹脂封止材で検査不正を公表
10月 KYB 免振/制振ダンパーで検査データの改ざんを公表
2019年
1月 IHI 無資格者による検査(無資格検査)が発覚
3月 ジャムコ 航空機の内装品で無資格検査と業務規程違反が発覚
4月 スズキ 燃費・排出ガス検査不正以外の検査項目の不正を報告
8月 菱三工業 産業機器用鋳鉄製品で品質データ偽装を報告
2020年
1月 デンソー 燃料ポンプの品質不適合で米国でリコールを届け出
2月 三菱電機 高耐圧パワー半導体モジュールで検査不正を公表
3月 デンソー 燃料ポンプの品質不具合で世界でのリコールに発展
4月 日立金属 特殊鋼・磁性材製品で検査データの改ざんを公表
9月 JSSJ シートベルトのベルト部分で強度データの改ざんが発覚
10月 三菱電機 車載ラジオで欧州無線機器指令の不適合品の出荷が発覚
10月 東洋紡 ポリエチレンテフレタレートのUL認証の取り消し
2021年
1月 京セラ 有機材料および機能性材料でUL規格不正を公表
2月 東洋紡 新たに3種類の樹脂でUL規格認証の取り消し
2月 曙ブレーキ 自動車ブレーキで品質データの偽証を公表
2月 小林化工 経口抗真菌薬への異種薬品購入で業務停止
3月 日医工 後発医薬品の不正な廃棄回避と試験の不実施業務停止
3月 東洋紡 さらに3種類の樹脂でUL規格認証の取り消し
4月 三菱電機 電磁開閉器関連製品でUL規格不適合が発覚
記憶にある案件もちらほらありますが、とにかく発生案件数の多さに驚きます。これらが「氷山の一角ではないこと(=全てであること)」を祈るばかりです。
・やっていないのにやったことにした。
・数値や結果を改ざんした。
なぜ、品質不正がなくならないのでしょうか?
2.東洋紡と京セラの事例
2021年10月UL認証取り消し問題に端を発した東洋紡での品質不正問題は21年2月、21年3月と芋づる式に出てきたに新たな品質不正案件にまで拡大しました(上記参照)。
調査結果によると、東洋紡で品質不正を是正する機会は何度もあったようです。にもかかわらず、それらに蓋をしてしまいました。「品質不正対象品の代替品を水面下で開発すること。」これを解決策とするという対応もあったようです。そうして不適合材料の販売を継続していました。
つまり、担当事業部で不正の事実は認識していたのです。こうなると問題点は、品質不正チェック体制云々ではなく、なぜほんとうのことを経営陣へ言えなかったのかに至ります。組織風土や文化、体質のことです。(出典:日経ものづくり2021年5月号)
2021年1月に発覚した京セラでの有機材料および機能性材料UL規格不正の長期の不適合および隠ぺいに終止符を打てたきっかけがあります。若手社員の悩みを工場長の明かしたことです。
ある若手社員が不適合材料の量産・販売について悩んでいると工場長に告白しました。2020年年11月のことです。
こうして翌12月、ようやく長年放置された不正の事実が担当事業部から経営幹部へ報告されました。勇気ある若手のお陰で膿を出せたわけです。もし、若手が勇気を奮わなかったら品質不正が放置されたままであったと推察されます。
問題の本質は経営陣へ悪い情報を伝えられないことにあったのではないでしょうか?(出典:日経ものづくり2021年5月号)
3.ある経営幹部の本気の決断
「ありのままの状況を報告してくれるようになりました。」
悪い情報も含めてありのままの報告が現場から届くようになったと感じている経営幹部です。これまでも現場のキーパーソンから報告自体はありました。各工程からの状況報告です。
しかし、経営幹部は何かが足りないと感じていました。報告者の本音が見えないのです。「自分の工程はしっかりやっていますよ」という説明に始終しています。
そこで、その経営幹部は、悪い情報も含めて本音の情報が現場から上がってこない理由を考えました。人時生産性向上活動を新たに始めたのがきっかけです。経営陣の言動を振り返りました。2つの点で誤った対応をしていたかもしれない・・・・・。
・仕事のやり方を直ぐに指示していた。現場のやり方に耳を傾けることはあまりなかった。
「〇〇はこうやれば上手くいくのでやってみろ。」
・その通りやっても上手くいかなかった場合、そのことを責める発言が多かった。
「なぜ、上手くできないのだ。」
こうした対応が、下記のような思考回路を各工程の管理者へ埋め込むことになってしまったのではないか?というのです。
上手くいかないと責められる=責められたくないので無難なことしかやらない=失敗はしていないという説明に始終する=本音は明かさない=悪い情報は包んで温める・・・。
「管理者を育成しているつもりでしたが、当人にしてみると責められているように感じていたのかもしれません。経営陣も言いたいことを言っていただけでした。ここは反省する必要があります。」
この経営幹部のスゴいところはここです。「経営陣のやり方に問題あり」と認識したことをきっかけに言動をがらりと変えました。言うは易く行うは難しです。なかなかできるものではありません。
しかし、その幹部はやったのです。言いたいことを我慢して、耳を傾けることにしました。すると、現場のキーパーソンから上がってくる報告内容に変化が出てきました。
「〇〇やったが上手くいかなくて困っている。」
「部下に指示したが動いてくれなくて悩んでいる。」
「▲▲するとできると思ってやってみたがダメだった。」
困り事、悩み事、失敗事の報告が届くようになりました。当然ですが、上手くいったことの報告も有ります。経営幹部は成功事例を評価する一方、困り事、悩み事、失敗事はオープンにしてプロジェクトチームで解決するように変えました。
担当者が一人で問題を抱えて悩む状況にさせないようにしたのです。周囲を巻き込み、チームで問題を解決する仕事のやり方に変えました。
優れた経営者や幹部は自身の言動を変えることに躊躇しません。全ては事業の豊かな成長発展のためです。目線の高さが違います。
工場経営で優先すべきはイイ情報ではなく悪い情報です。タイムリーな対応をしないと、企業の存続を危うくするような事態に陥らないとも限りません。悪い情報とはそう言うものです。
事の是非は全てお客様が決めます。お客様にとって我が社の都合は関係ありません。だからこそ悪い情報は直ぐ現場から上がるようにしなければならないのです。
悪い情報が上がって来ない原因は経営者や幹部の言動にあります。現場ではありません。貴社は大丈夫ですか?
4.トヨタのアンドン
トヨタの生産現場にはアンドン」があります。異常を見つけた作業者が自らラインを止めるシステムです。ラインを止めるとベテランが駆けつけてくれます。ベテランが問題の処置をするのです。
ベテランは異常を見つけてくれた作業者へ声を掛けます。「ラインを止めてくれてありがとう。」
これがトヨタの「自働化」、ニンベンのついた自働化です。異常品は絶対につくりません。その場で解決です。
ただし、作業者が異常だと判断してラインを止めたとしても、ベテランが調べたら異常ではない場合もあります。この場合、ベテランはその作業者へどう対応するのか?
トヨタでは次のように対応するのです。
調査して、もし異常がなかったら、「これは異常ではない。」と指導するだけです。「なぜ止めたのだ?」とは絶対に言いません。異常も無いのに止めたことを責めないのです。止める必要がないことを指導するだけです。指導するけれども叱りません。
こうしたベテランに導かれた現場は異常を察知するセンスが高まります。失敗しても、失敗した背景を説明してくれるのです。責められないのです。
仕事に挑戦しようという雰囲気が自然と生まれます。こうした現場なら、作業者や管理者は悪い情報を優先して上層部へ届けなければならないとの想いを抱くことでしょう。責められないのですから。
チームはそれを率いるリーダーの言動次第です。リーダーは問題が発生したときに原因は追究するけれども犯人捜しはしません。
(出典:日経ものづくり2021年7月号)
5.プロ野球日本シリーズを制したヤクルト高津監督の「絶対大丈夫」
先月のプロ野球日本シリーズはまれに見る接戦でした。優勝はヤクルト。20年ぶりの優勝です。高津監督は就任2年目。前シーズン最下位からの大躍進でした。
高津監督(53)は、「絶対大丈夫」を合言葉でチームを引っ張ったそうです。野球解説者が次のように解説していました。
「監督が代わるとチームも変わるものです。」
チームとはそういうものではないでしょうか?だからこそトップの仕事振りが重要となります。プロ集団でさえ、トップの導きでパフォーマンスが激変するのです。ましてや、私達、中小製造現場のチームではどうでしょう。経営者の言動、一挙手一投足が現場に影響を与えるは当然のことです。
高津監督は次のことを語り続けました。
「周りのチームメートを信じ、チームスワローズが一枚岩でいったら絶対崩れることはない。絶対大丈夫。」
高津監督の言葉を耳にし続けた選手がどう感じるか?プロの選手でもそうなのです。経営者の言葉が雰囲気をつくり、人を動かします。しばしばお伝えしている日本古来の「言霊」という考え方です。
経営者の確信を持った言葉が現場を動かします。経営者の言葉が現場の雰囲気づくりに重要な役割を果たすのです。
6.品質不正を未然に防ぐ唯一の方法
品質不正問題も、当然に、トップの言動が大きく影響します。長年、積み重ねてきた歴史の結果できあがるのが組織風土や文化、雰囲気です。
問題発覚時点の経営者だけが悪かったと言えない事情があるかも知れません。しかし、誰かが負の連鎖を断ち切らなければなりません。トップにしかできない仕事です。
中小製造経営者は大手ほどの組織規模を背負っていませんが、それでも企業独自の組織風土のもとで経営をしていることに変わりはありません。風通しが悪いと感じたら、ご自身の言動を振り返り、とにもかくにも悪い情報が「普通」に上がってくる現場へ変える必要があります。
多品種少量生産、マスカスタマイゼーションなどなど、ものづくりが複雑化するのは回避できない時代の流れです。現場がトラブルや困り事に直面する事が増えます。悪い事は「芽」のうちに摘み取らなければなりません。そのためにも悪い情報が「普通」に上がってくる現場をつくりたいです。
7.スローガンにしては絶対ダメ
品質不正を未然に防ぐのは経営者の言動です。これしかありません。安全・品質を工場経営の最優先項目に掲げるのは経営者にしかできないことです。
さらに、これを実践項目にするか否かも経営者の言動次第なのです。スローガンにしては絶対ダメです。実践項目にしなければなりません。ご自身の言動を振り返ってください。