戦略的工場経営ブログ運搬工程分析では先入れ先出しの置き方に注目する
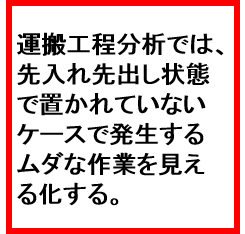
運搬工程分析では、物が、 先入れ先出し状態で置かれていないケースで発生する ムダな作業を見える化する、という話です。
1.マテハンのマクロ的およびミクロ的視点
工場で付加価値を生み出すのは唯一、加工工程のみです。 重い荷物を一生懸命、汗をかきながら運んでも、顧客視点では 加えられた価値はゼロです。 当事者は頑張ったのになんともモッタイナイことです。 そこで、価値を生み出さない作業は、 マテリアルハンドリングとして捉えます。 そして、その作業がなぜ発生するのか、作業の存在自体の 必然性から3つの視点で分類しカイゼンを考えます。 A)戦略的に必要なバッファでのマテリアルハンドリング B)滞りのない流れのために必要なマテリアルハンドリング C)原則的にゼロを目指すマテリアルハンドリング (マテリアルハンドリングを3つの視点で分類する) まず、マクロ的にマテリアルハンドリングを分類します。 全てのマテハンが無意味であるというわけではありません。 戦略的に経営者が必要であると判断するならば、 そのマテハンの位置づけは高まります。 ですから、まずは、なぜその作業が発生しているのか? この視点が欠かせないわけです。 分類した後、具体的な個別のマテハン分析、改善に移ります。 ミクロ的な取り組みへの移行です。 マテリアルハンドリングでは、 あらゆる物の移動、積み下ろし、貯蔵、出荷など、 品物の取り扱いを対象としています。 そのうち、多くの現場で議論となるのは「移動」です。 つまり「運搬」です。 機能別レイアウトが多い中小の現場では、 頻繁に運搬作業が発生します。 また、製品別レイアウトの場合でも、 工程間がコンベアなどの搬送装置でつながっていない限り、 人力やフォークリフトでの運搬作業が発生します。 日常的に発生している運搬作業。 今日も現場を爆走(?)しているフォークリフト。 あるいは、製品を持って右往左往している工程管理者。 まずは、運搬作業の”今”を知ることから始めます。2.運搬分析
運搬改善に用いられる分析手法はいろいろありますが、 ここでは代表的な3つの手法を上げます。 1)運搬工程分析 2)運搬活性化分析 3)カラ運搬分析 運搬分析は、その分析自体で意外な発見ができるというよりは、 現場で感覚的に”問題だなぁ”と認識している現象を数値化、 見える化する役割が多いように感じます。 ですから、問題の発見者が、その問題の重大性や改善後の効果を、 他のメンバーへ伝えるのに使えます。3.運搬工程分析
運搬工程分析は、一般的な工程分析と手法は同じです。 物が運搬され、たどった経路を明らかにします。 比較対象は正規工程のルートです。 原材料や購入部品をラインへ投入してから後、 加工や組み立ての各工程を経て製品になる。 その後、出荷されます。 この正規ルートと比較するのです。 ですから、運搬工程分析では、模式的な表現よりも、 実際のレイアウト上での物の動きを示した方が、 感覚的な理解が進みます。 仕掛品として滞留し、キズ等で手直しを行えば、 正規ルートから外れます。 この外れた状況を見える化するのがポイントです。 ただし、こうした状況は、特別に分析をしなくても、 把握できていることです。 わざわざ分析と称して、時間を割いて整理するほどのことでは なさそうです。 ですから、運搬工程分析で明らかにすべきは、 正規ルートから外れたルートの先での、 一時的に滞留している状況です。 具体的には、物が先入れ先出し状態で置かれているか否かです。 つまり、正規ルートから外れ、一時的に保管する場所で、 物の出し入れの手間がかかるのか、かからないかです。 先入れ先出し状態で置かれていない箇所を特定していきます。 図1は「先入れ先出し状態で置かれていない」ケースです。

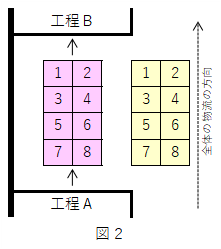
