戦略的工場経営ブログ不良品の「率」ではなく、「額」に注目する
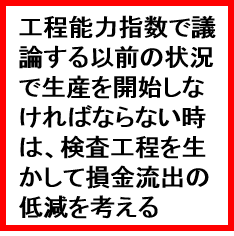
貴社では不良品が発生したとき、まず、何に注目しますか?
1.検査コストを忘れない
工程能力指数は検査コストを見極める手掛かりになります。 要求品質は維持しなければなりませんが、かけられるコストは青天井ではありません。 判断基準が必要です。 ですから、お客様の要求品質を維持するための「最低の」検査コストを見極めます。 (工程能力指数1.33で最低必要な検査コストを知る) 工程能力指数1.33水準の生産工程では、製品仕様次第で抜き取り検査が可能です。 10万個で不良品の発生が6個程度の品質水準です。 顧客との合意の上で、抜き取り検査で品質を保証する体制を構築することもできます。 抜き取り検査の検査コストは、全数検査に比べて有利です。 工程能力指数は、検査コストに関する客観的な判断基準になるのです。 ですから、新製品の量産を立ち上げるときには、可能な限り品質を上げておきます。 工程能力指数を向上させると、不良損金に加えて、検査コストの面でもメリットがあります。 製造原価には検査コストが含まれています。 しかしながら、新製品開発の際、 検査体制や検査コストの検討が十分になされないことがたびたびあります。 モノづくりに専念しすぎて、検査工程の検討が後回しになるからです。 工程能力指数を新製品開発DRの評価項目に入れておけば忘れません。2.継続的な不良品対策はモノづくりの根幹
新製品を立ち上げる現場としても、工程能力を議論できる品質水準が欲しいところです。 品質水準が高ければ検査コストを低減できる可能性があります。 さらに、品質水準が高いということは、生産計画どおりに進捗する見通しも高くなるからです。 しかしながら、いつも品質水準が高い状態で量産を迎えるとは限りません。 工程能力指数で議論する以前の状況で、生産を開始せざるを得ない製品もあります。 こうした製品では、不良低減の取り組みに全力投入です。 量産をしながら、不良品対策を推進します。 生産現場における継続的な不良品対策はモノづくりの根幹をなします。 自社工場のモノづくりノウハウの多くはこの活動を通じて得られるからです。 生産性や品質の面で、日々の生産活動を支援する継続的な活動がある現場は強いです。 地道な生産活動を科学的に検証する場を持つからです。3.儲かる工場経営で注目するのは率ではなく額
不良対策の判断基準は不良損金額です。 不良品発生による損金を多寡で判断し、その低減を最優先に定めます。 多種多様な不良品を目の前にして判断すべきは、不良損金額です。 不良率ではありません。 「率」ではなく、「額」です。 最終的には不良率の低減を目指します。 ただし、まず、考えるのは「不良損金」の低減です。 最初にやるべきことは、不適合品が原因でお金が無駄に流出するのを止めることです。 不良率の低減活動はその次になります。 不良率低減には、工学的な課題に対応しなければならないこともしばしばです。 対策実施まで時間を要することがたびたび。 それまで、「不良損金」を垂れ流しにするのか・・・・。 そこで、検査工程を加えるのです。 「不良損金」の流出を低減できないかを検討します。 不良の原因が、 不良品を認識した工程よりも前方の工程にあるならば、ひとまず不良損金を低減できます。 検査工程を加えることで、不良品に累積される製造コストを抑制できるからです。 製品1個当たりの検査コストと不良損金と比べて判断をします。 具体的な事例で検証します。 工程Aと工程Bから構成される生産ラインを仮定します。 検査工程が工程Bの後ろに設定されています。 100個生産して20個の不良が発生しました。
