戦略的工場経営ブログ標準作業を持たない現場はスマートにはなれない
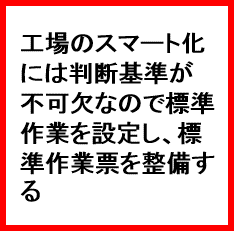
工場のスマート化には判断基準が不可欠ない。 標準作業を設定し、標準作業票を整備する、という話です。 現場に作業標準票は整備されていますか? ウチにはベテラン作業者が多いから、それほど必要性を感じないなぁ。 ただ、彼らが引退する時期までに標準化を進めないといけないだろう・・。 急いで標準化を考えねばならない理由はあるだろうか?I IOTを活用したかったら、必要なのです。 技能伝承の観点ではありません。 今を知る、今を把握するという観点でも標準化が必要なのです。 測定基準(判断基準)という視点で考えても欠かせません。
1.工場自動化と情報通信技術の融合で自社工場を変える
インダストリー4.0はドイツ政府が主導する国家的な技術戦略です。 (IOTに乗り遅れないためにやっておくべき2つのコト) 産官学が一体となって「スマート工場」の実現に取り組んでいます。 スマートという表現は、 「細身の」とか「すらっとしている」のようにスタイルに関連してしばしば耳にします。 IT関係では、原義の「賢い」、 「気が利く」から転じ、 「情報化された」、「高度な情報処理機能が加わった」等の意味で使われています。 「スマート工場」のスマートは 「情報化された」、「高度な情報処理機能が加わった」と解釈します。 つまり、工場自動化(FA)と情報通信技術(ICT)が融合した工場です。 ところで、FAとICTが融合した工場のイメージって???????? よくワカラン!!です。 生まれたてのコンセプトでもあり、現在その解釈はいろいろです。 ただはっきりしているのは、次のようなことです。 会社視点、工場視点でのモノづくりが優先される時代は終わりであること。 顧客視点で高付加価値製品をいかに効率よく顧客に届けるか争点になっていること。 そしてそれが、地球規模で起きていること。 そして、それを実現させるための「スマート工場」であるということ。 そこでは工場内外がインターネットなどの通信ネットワーク技術でつながっている。 キーワードは「つなげる」ことです。 工場内の装置同士をネットワークでつなげる。 工場と営業所と顧客をインターネットでつなげる。 つなげることで新たな価値やビジネスモデルを創出する。 こんな感じです。 中小モノづくり工場で存続と成長のために必要なのは付加価値の新たな創出です。 そこで取り組むべき課題の方向性は2つです。 1)製品のカスタマイズ化(マス・カスタマイゼーション) 2)納期短縮(超短納期化) (マス・カスタマイゼーションで付加価値を拡大させる) (中小企業の強みを生かし超短納期に挑戦する) そして、この2つの課題を解決する手段に、「つなげる」があげられます。 ですから、今後、自社工場でも大いに「スマート工場」目指します。 そこで、まず、下の2つのことを考えます。 1)自社工場の現在の問題点と未来に向かって目指すべき状態は? 2)工場自動化と情報通信技術を融合させると自社工場をどう変えられる? 漠然としていたことをハッキリさせます。2.「今」を知らなきゃ進化のしようがない
まずは、中小モノづくり工場がIOTの流れに乗り遅れないためには、次の2つが必要です。 1)人財の自立性を評価する仕組みを構築すること。 2)今の自社工場の設備をトコトン使い尽くすこと、知り尽くすこと。 (IOTに乗り遅れないためにやっておくべき2つのコト) このうち後者は、「今」を知る、把握することが狙いです。 自社工場をカイゼンし進化させるには、 現状の立ち位置を客観的にハッキリさせておくことが不可欠です。 なぜなら、カイゼンする、 進化させる、前へ進める、という行為は相対的な行為だからです。 設備投資で上手くいかなかったなぁ、 という場合、その原因のほとんどは、現在の立ち位置の把握不足です。 ですから、この「今」を知ることは自社工場をカイゼンして進化させるために必要です。 これ抜きにカイゼンしてもしょうがないです。 そして、その現状の立ち位置に関する情報が「標準作業」です。 ここに現場のすべてのノウハウが詰まっています。 現場の生産活動を「見える化」します。 現場の暗黙知を形式知へ変換するとも表現されます。 自社工場には標準作業票が整備されていますか? さて、IOTを導入することで自社工場をどのように変えることができるでしょうか? 例えば、「設備トラブルの認識とその自動復帰」のアイデアが浮かびます。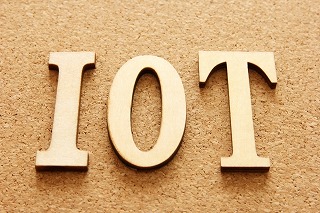
3.アメリカで出版された「KAIZEN」:標準が欠かせない
1980年代にアメリカの出版会社から 「KAIZEN」という書籍が刊行されました。 この書籍をきっかけに欧米でカイゼン・ブームが起きました。 日本の製造業の強さが世界に理解され始めた頃です。 著者である今井正明氏はその中で次のように語っています。標準のないところにカイゼンはない。 いかなるカイゼンも、その出発点は、現在の立脚点である。 あらゆる作業者、あらゆる機械、 あらゆる工程に適用される正確な測定基準が必要である。 同様に、すべての管理者にとっても測定基準が必要である。 TQCおよびカイゼン戦略を 導入する以前の段階でさえ、 会社がどこに立脚しているか、 現在どのような標準体系があるかを理解しようとつとめるべきである。1980年代の書籍ですが、全然、色あせていません。 それどころか技術が高度化する中、現場で忘れられている勘所を思い出させてくれます。 全くそのとおり!!と膝を打ちたくなる記述にも出会えます。 標準のないところにカイゼンはない、と断言しています。 測定基準は判断基準と読みかえても全く同じです。 さらに注目すべきは「カイゼン戦略を導入する以前の段階でさえ、・・」の部分です。 つまり、会社経営や工場運営にはそもそも測定基準(判断基準)が必要ということです。 (これからは判断基準となる指標の活用を考えるべき)(出典:カイゼン 今井正明著)
4.IOTでのテータ活用事例:やっぱり標準がなければ進まない
工場のスマート化を目指す企業に 「FOA(Flow Oriented Approach」という手法が広がっています。 (日経ものづくり2015年9月号) 元ブリジストン常務執行役員で 現在smart-FOA代表取締役社長の奥雅春氏が考えた手法です。 スマート工場では、 従来と比べて大量のデータが生み出されます。 昨今、ビックデータという言葉をたびたび耳にします。 そのデータを、「現場」で 使いやすい形にするにはどうしたらイイか、という点に着目した情報システムです。 従来のデータベースとの違いを、次のように説明しています。従来の考えでは、現場から生み出された大量のデータを分析して知見を得る。 それに対して、FOAでは 現場が使いやすいように 生データに「背景データ」と「説明データ」 を加え、問題の因果関係を類推しやすくし、適切な行動をとりやすくする。現場が使いやすいようにするため、データベースの様式を工夫した、ということです。 その奥氏はさらに次のように語っています。
「現場で問題が起きるのは、だいたい4Mのいずれかに異常が生じたとき。 その変化を捉えるには、事前に標準を決めておかなければならない。」現象の因果関係を見出すうえで重要になるのは「標準」の状態をきちんと定義しておくこと。 「標準」抜きに、生データに付加された「背景データ」や「説明データ」は生きないのです。 つまり「標準」がなければ機能しないのです。 やっぱり、「標準」です。 ここで、 「工場のスマート化で重要なことは何か。」という質問への回答結果を下記に示します。 (出典:日経ものづくり2015年9月号) 対象者は224名メーカー関係者です。
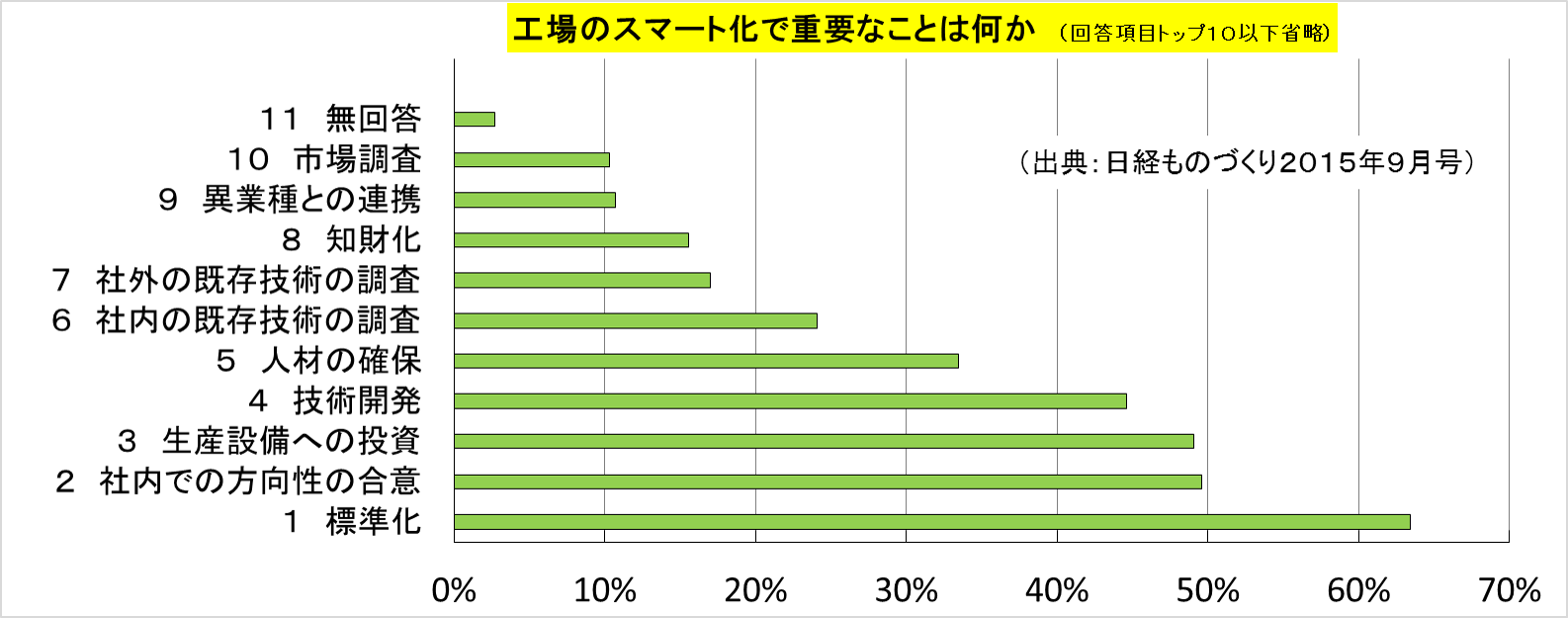