戦略的工場経営ブログ多品種の混沌とした”大海”を分類する着眼点
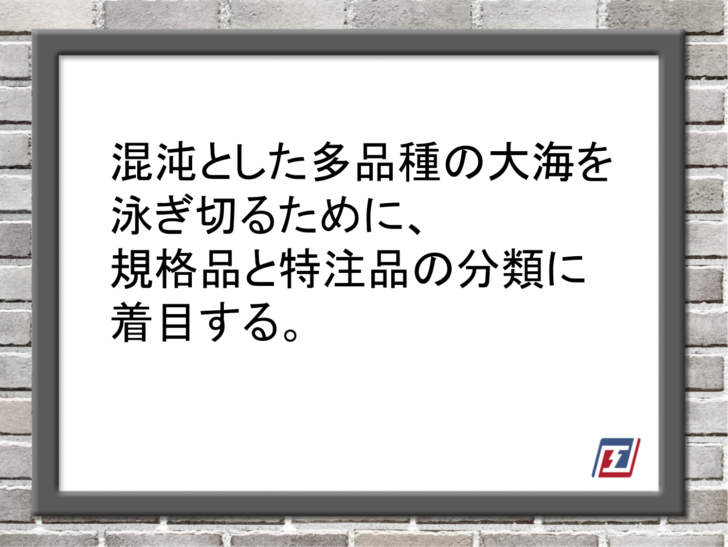
貴社の製品を分類する観点、ありますか?
1.製品の流れ分析をするときに直面する問題
弊社では、生産管理の視点から、儲かる工場経営の仕組みづくりを進めます。
モノづくりを通じて、満足度が高まる価値を顧客へ提供し、その対価を得るのが製造業です。
そして、その価値の多くはスムーズなモノづくり、滞りのないモノづくりから生み出されます。
行ったり来たり、
出たり入ったり、
あっちこっちに停滞が見られるモノづくりでは、顧客へ届ける価値が毀損する感じがしませんか?
儲かる工場経営の根幹は、滞りないモノづくり、つまり生産の流れをつくることに他なりません。
したがって、
儲かる工場経営の仕組みづくりでは、
生産の流れを阻害する要因の除去が論点となります。
ここで、阻害要因を探る観点のひとつがボトルネックです。
製品を特定し、その製品の流れ分析を行います。
活用する手法は、生産管理3本柱のうち、工程管理の考え方です。
工程管理では、手順計画、工数計画に
したがって工程を設計し、そこを流れる製品の流れ方をチェックします。
ただし、多くの中小現場では製品の流れ分析をどのようにやればいいのだろうか?そのやり方がわからない!という問題に直面しているようです。
まず問題となるのは、流れ分析の対象製品を選択できないということです。
したがって、調査対象になる製品の選択基準を決めなければなりません。
どの製品に着目して、阻害要因を洗い出すのだ?
この問題で頭を悩ませる現場が少なからずあります。
何を基準に調査すべき製品を選択すればいいのでしょうか?
貴社にはその基準がありますか?
2.ある企業の設計担当者がやったこと
多くの中小現場では、扱う品種が徐々に増えてています。
あるいは、
品種はそれほど変化していないけども、
短納期化してきた、
受注情報がころころ変更される、という状況になっています。
少品種多量生産であるなら、
品種が少ないこともあり、
現状把握の難易度はそれほど高くはありません。
分類する観点が限定的であり、
量的な対応には統計学的手法があります。
しかし、少品種多量生産の手法をそのまま適用できる中小現場は稀です。
多品種少量、変種変量の生産となっています。
そうした現場では、
どの製品に着目して、生産の流れの阻害要因を見つければいいのか判断ができない!
という問題にぶち当たってしまいます。
ここで活用できる考え方にグループテクノロジー(GT)があります。
多品種少量生産の生産効率を高めるため、製品を寸法、形状、材質、加工法などで分類します。
多品種製品の標準化のやり方のひとつです。
製品の特徴に着目して、調査対象の製品を選択、その製品での阻害要因を分析します。
ただし、GTによる手法があるものの、現場ではそう簡単に適応できないのも事実です。
あるクライアント企業様先でのことです。
設計担当者へ「製品の分類をしたことがありますか?」と尋ねたことがあります。
担当者の答えは次のようなものでした。
「やったことはないですね。
うちの製品は大きさも形も千差万別で、
工程をスキップするタイプもあって複雑すぎます。」
こうした回答はしばしば耳にすることです。
ただし、千差万別と言っても、
寸法、形状、材質、加工法など、なんらかの着眼点を見つければ、分類は可能はずです。
無限ということはありません。
しかしながら、
日々の忙しい業務の中で、
複雑に絡み合った糸をのように
混沌とした多品種の”大海”を泳ぎ切って、
全体を俯瞰することはそうたやすいことでもありません。
GTでは、
モノづくりの観点で
分類する切り口を提示していますが、そもそも、選択肢が多すぎます。
そこで、生産の観点で分類するのです。
生産の頻度が多い、少ない。
生産量が多い、少ない(P-Q分析)などなど。
弊社でしばしば、活用する観点は、規格品と特注品です。
規格品とは、
数量は変動するものの
一定間隔(例えば毎月)で、
注文がある一定期間(例えば2~3年間)、継続的に注文が届く製品。
現場では繰り返し品、リピート品とも言われます。
一方、特注品とは、その注文限りの製品。
過去実績をこの規格品と特注品に分類するのです。
そうして、規格品に焦点を絞って、分類をします。
まずは、規格品を対象に分析を進めるのです。
毎月、繰り返し、現場に登場する製品なので現場から情報を集めやすいという利点もあります。
分類された規格品をさらに、生産数量、売上高などの観点で分類するのもひとつのやり方です。
さらに、この段階でGTの手法を使うこともできます。
先のクライアント企業先でもやってみました。
「繰り返し品である、このアイテムから調べてみます。」
先の担当者も調査を進める切り口を見つけたようでした。
3.規格品と特注品
生産の流れをつくるため、規格品に着目するのは、ひとつのやり方です。
1回限りの特注品とは異なって、
現場に登場する頻度が多く、
改善活動の成果が波及する領域は広くなります。
成果を実感しやすいというのは、
やる気を引き出す3つのポイントである有能性に働きかけられるのです。
複雑に絡み合った糸のように
混沌とした多品種の”大海”を泳ぎ切る着眼点として、現場へ登場する頻度に注目します。
製品分析のため、規格品と特注品に分類する仕組みをつくりませんか?