戦略的工場経営ブログ開発業務で中小現場の強みを生かす2つのポイント
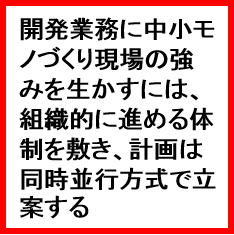
開発業務をQCDで測っていますか?
1.モノづくり力と人財力はQCDで測られる
製造業での競争力はQCDで測られます。 品質、コスト、納期です。 生産現場ではこれらを見える化し、情報共有しながら改善を重ねます。 モノづくり力と人財力を高め、市場における持続的優位性を構築する戦略が欠かせません。 モノづくり力と人財力は競争力の源泉であり土台です。 日々の生産活動の仕組みがしっかりしていない現場は脆弱です。 製造現場の豊かな成長にはイノベーションが欠かせません。 改善活動による積み上げ式の漸進的進歩は重要な役割を果たしています。 しかし、それだけでは外部環境の変化についていけないでしょう。 ブレークスルー、つまりイノベーションも必要です。 そのためには継続的な研究開発も欠かせないのです。 研究開発のような将来投資をやりきるにはモノづくり力や人財力がカギとなります。 日々の生産活動の仕組みがしっかりしていない現場では期待できません。 こうした状況で技術開発を進めようとするのは、 ぬかるんでいる地盤に杭を打ち、その上に家を建てようとするようなものです。 時間の経過と共に確実に家は傾き、果ては崩れ落ちます。 その技術開発と製品開発の土台になるのが日常の生産活動です。 つまり現場が有するモノづくり力であり人財力です。 そして、モノづくり力と人財力はQCDで測られます。2.開発業務QCD
生産現場のモノづくり力と人財力はQCDで測られます。 したがって、技術開発と製品開発の競争力もQCDで測ることができます。 中小の現場では片手間で、研究開発や試作をやっていませんか? これではだめです。 開発納期を設定して全員で開発業務の位置づけを共有することから始めます。 QCDのDの設定です。 さらに、企業の存続と成長には、 日々の生産活動だけではなく、 長期的な視野に立ったイノベーションが 不可欠であることを全員で認識します。 中小と言えども、 生産活動に加えて、 技術開発や製品開発もやらねばならないのです。 日々の生産活動だけでなく、研究開発でも競争力を高める必要があります。 研究開発もQCDの観点で評価するのです。 開発品質、開発コスト、開発納期。 開発業務もこれらQCDで競争力を測ります。 品質には設計品質と製造品質(適合品質)があります。 これらを決定するのが開発品質であり、両者の最大化を目指します。 製造品質を最大限に考慮し、製造容易性、組立容易性に優れた製品を開発することは大事です。 しかし、製品の商品価値が低く、顧客に選ばれなければ、売上高増に寄与することができません。 一方、商品価値が高く、 顧客に選ばれる商品が開発できても、 現場にとって造り難く、 不良品の発生率がとんでもなく高ければ、 売上高が伸びる割には利益が増えない状況に陥ります。 両者の品質のバランスを決定するのが開発品質です。 また、開発納期を考慮することは開発コストを低減することにもつながります。 納期を設定することで業務全般の効率を上げ、コストも抑えることができます。 中小モノづくり現場の経営資源には制約条件がたくさんあります。 限りある人材の中で、 開発業務を進める上で大切なのは、 生産活動と同様にQCDを見える化した開発業務を進めることです。 見える化で開発業務における現場の当事者意識を引き出すことができます。 そもそも開発業務は、不確実性の高い仕事です。 それだけに、進めるべき方向性のイメージが欠かせません。 開発業務が上手くいっていない中小現場のほとんどは情報が見える化されていません。 開発業務を客観化することが大切です。 生産活動と同様に開発業務QCDの見える化を図ります。3.中小モノづくり現場の強みを生かす2つのポイント
中小現場での開発業務では現場の強みを生かしたいです。 2つのポイントがあります。 ・開発業務を組織的に進める体制にする。 ・開発計画は同時並行方式で立案する。 この2つです。 中小現場では、開発業務の専任を置くことができないことが多いです。 したがって、 ・トップ自ら一人で進めるケース ・設計部門の担当者が兼務で進めるケース こうしたケースが多く見られます。 これでは組織の強みを生かせません。 開発計画が業務A→業務B→業務C→業務Dというように、業務をリレー式になりがちです。 つなぐ形式にならざるを得ません。 ひとつの業務が終わるまでに、次の業務を進めることが原則、困難です。 時間がかかります。 リスク管理として、多様な場面を想定して幅広く、場合分けした業務を設定できません。 1人では限界があります。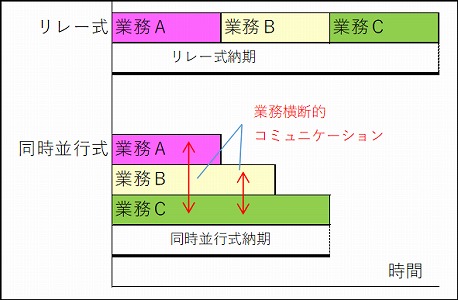