戦略的工場経営ブログウェアラブル・デバイスは現場に受けそうな気がする
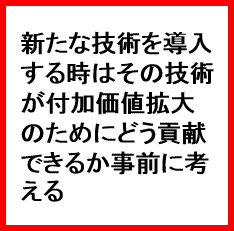
新たな付加価値を生むためにどのような貢献ができるのか? 新技術を導入するときにしっかり考える、と言う話です。 ウェアラブル・デバイスのような新たな技術の導入を検討したことがありますか? 技術導入にあたっては、事前に狙いと目的をはっきりさせます。 ウェアラブル・デバイスを付加価値創出に活かせないか、という視点で考えます。
1.ウェアラブル・デバイスは現場に受けそうな気がする
ウェアラブル・デバイスがモノづくりの現場で使われ始めています。 ウェアラブル・デバイスの身近なところではApple Watchがそうです。 それと、発売当初、話題になったGoogle Glassなどもそうです。 モノづくりの現場では、 ヘッドマウント・ディスプレー (目の前に小さなディスプレーが見える)、 ウェアラブルカメラ、 音声認識端末、 ウェアラブルグラス等々が導入され、効果を出し始めています。 こうしたデバイスはハンズフリーで使えます。 作業者は作業を中断することなく、情報を「発信」したり、「受信」したりできます。 様々な使い方が期待できます。 「作業を中断することなく」という利便性に注目です。 現場へ定着する可能性の高さを物語っています。 とにかく現場は忙しいです。 生産のための作業が、当然に優先度一番です。 ですから、どんなに役に立とうが、 どんなに効果があろうが、 生産のための作業に影響を及ぼし、 作業の負荷を増やすことは、 現場へ定着しません。 しかし、このウェアラブル・デバイスは違います。 作業負荷は変わらず、メリットだけを作業者に提供してくれます。 こうしたモノは現場に定着しやすく、自然に広まります。 現場の目的と合致した使い方をすれば大きな効果を期待することができます。 現場毎の独自の使い方がカギです。2.iPhoneも最初は誰も楽しみ方を知らなかった
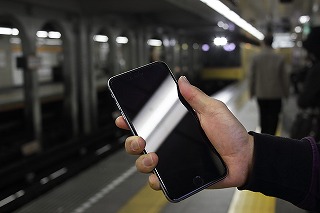
2-1 マスカスタマイゼーションのために使えないだろうか?
例えば、マスカスタマイゼーションの課題は? とにかく品種が多いです。 従来の品種が100~200程度として、 それが2倍、3倍、あるいは一桁多くなることもあり得ます。 顧客が驚くほどの、 前例がない水準の多品種に対応できてこそ、 マスカスタマイゼーションでの独自性、尖鋭性を打ち出せます。 中途半端ではダメ。 そうなると、同時に、 それだけ多くの品種の標準化(標準作業、標準時間)も必要になってくるわけです。 標準化の作業工数を考えるとウンザリ・・・・、となります。 そこで、ウェアラブル・デバイスを標準化作業の効率化に活かせないかと考えるのです。 ウェアラブル・デバイスを標準化のコンテンツ作りに使って効果を出している事例があります。 パナソニックの群馬大泉工場、セル生産ラインです。 (出典:日経ものづくり2015年10月号) 4kウェアラブルカメラで撮影した実際の作業映像から標準作業書のコンテンツを仕上げています。 その結果、下記のような利点を上げています。・ウェアラブルカメラは作業者が装着するので、従来のような撮影者が現場に張り付く必要がない。 ・映像が作業者目線なので、手元やワーク等、必要なモノが必ず映る。 ・従来の映像では作業者の正面から撮影していたので、作業者の視点とは左右が逆であったが、それがない。 ・手が邪魔になって映らない部品、治具の別撮りの手間が省ける。 ・従来コンテンツ作成に1製品につき丸1日かかっていたが、今は1時間程度で済む。なるほど。 現場の標準化が進み難い原因のひとつに、標準書をつくる負荷が大きいことがあります。 私も現場作業の標準書をいくつも作成しましたが、まぁ手間がかかります。 現場に張り付き、作業内容をメモし、作業内容、手順を整理、そして時間計測して標準時間を評価し・・・。 ですから、道具を使って標準書の作成効率が上がるならば大いに活用されます。 また、映像コンテンツとしても標準化を進められます。 さらに、映像へ音声データを加えて使えます。 文面での標準作業書は記述項目全体を一目で把握するのに優れています。 そこに音声や映像など、五感に訴えかけるコンテンツを加えるるのです。 標準署の内容が、現場へ伝わりやすくなります。 多品種化が進む中で、正確で精度の高いコンテンツを効率よく作れます。 標準書の作成負荷が低減する上に、分かりやすいコンテンツに仕上げられます。 標準書を作成している現場にも大きなメリットとなります。 また、使用する側の立場に立って考えても、大きな利便性があります。 文書を持ち歩かなくてもイイということです。 現場で作業標準書を参照する時、いちいちファイルを持ち出さねばならない手間があります。 現場で仕事をしていた新人エンジニア時代のときのことです。 現場に持ち出しては、しまうのを忘れることがしばしば。 現場責任者(当時は組長と言っていました)に何度も怒られたことを思い出します。 いすれにせよ、持ち歩くのは面倒です。 また、現場作業者にしても、 現場での作業時にこの作業標準書を手元において、 見ながら作業を・・・、 ということを普通はやりません。 なにせ、現場では邪魔です。 ですから、 詰め所で目を通して”記憶”して作業に入る、というのが多くの作業者のやり方でした。 それを、 ひとりひとりが身に着けたデバイスを通じて、”気軽に”見られたら使いやすいです。 さらに、 それが文書だけでなく、映像や音声によるコンテンツでもあったら、理解もしやすいです。 そのような標準書ならば「普通」に活用したくなります。 多品種少量化の流れは避けられません。 マスカスタマイゼーション対応も求められます。 したがって、目前の製品の種類・仕様がドンドン変わる環境に現場は置かれます。 ミスを回避するためには、標準書をいやでも確認しなければなりません。 「超」多品種化では標準書を効率的に機能させる工夫が不可欠です。 その時、「普通」に使える道具があれば現場は助かります。 先のパナソニックの群馬大泉工場では、ヘッドマウント・ディスプレーを活用しています。 作業指示を読み取るデバイスとして使っているのです。 視界内に小型のディスプレーが映し出されます。 作業指示を確認する際は、首を振らなくても視線を少し移動させるだけで見えます。 作業を中断することなく、作業指示の内容を確認できるのです。 現場で活用してみたくなります。(出典:日経ものづくり2015年10月号)
2-2 超短納期化のために使えないだろうか?
また、超短納期化での課題は? 対象製品の進捗情報を現場で共有することが、今まで以上に欠かせません。 毎朝ミーティングでその日の生産計画を確認しますから、生産の大きな流れは把握できます。 現場リーダーと各工程のキーパーソンは大きな流れを共有します。 ただ、品種も増えた中で、時々刻々と変化する現場に対応しなければなりません。 それも、短納期に対応しなければならないのです。 今日の朝イチから始めて夕方には発送する超短納期製品の突発受注を想定します。 受注情報を受けた時、各工程のキーパーソンは、何を考えるでしょうか? まさに今、この瞬間での前後工程の状況、および全体の進捗状況を知りたくなります。 各工程のキーパーソンは、こうした状況を知るために、情報が欲しくなります。 生産計画に変更がある場合、 あるいは、 突発特急の仕事が加わった場合、 生産管理担当者が、 各工程のキーパーソンに直接に声掛けをして伝達・フォローをすることが一般的です。 ただし、ここでの付加価値は「超短納期」です。 従来の仕事のやり方では追い付かず、間に合わなくなります。 現場の自律性に任せてこそ、実現可能な業務です。 生産管理者あるいは現場リーダーは状況把握につとめる。 そうして、必要な情報を各工程のキーパーソンへ、逐一発信する。 その情報を現場のキーマンは、腕時計型等のデバイスで確認する。 自工程がやらねばならないことを、時々刻々把握し実行する。 ストレスなく、タイムリーに情報を現場へ伝達することがキモです。 そのための道具としてウェアラブルデバイスは適しています。 当然、現場の自主的な判断を尊重する仕組みも不可欠です。3.まだまだ高価なデバイスなので、狙いや目的を明確にする
こうしたデバイスはまだまだ高価です。 バッテリー寿命など実用化に向けての課題は多いです。 しかし、将来、必ず現場で活用されます。 いかにも未来のモノづくりという雰囲気です。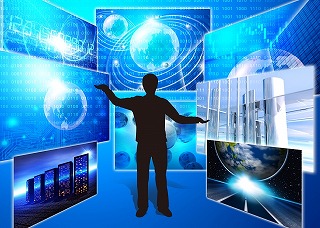