戦略的工場経営ブログ戦艦大和の生産管理:人時生産性向上へのヒント1
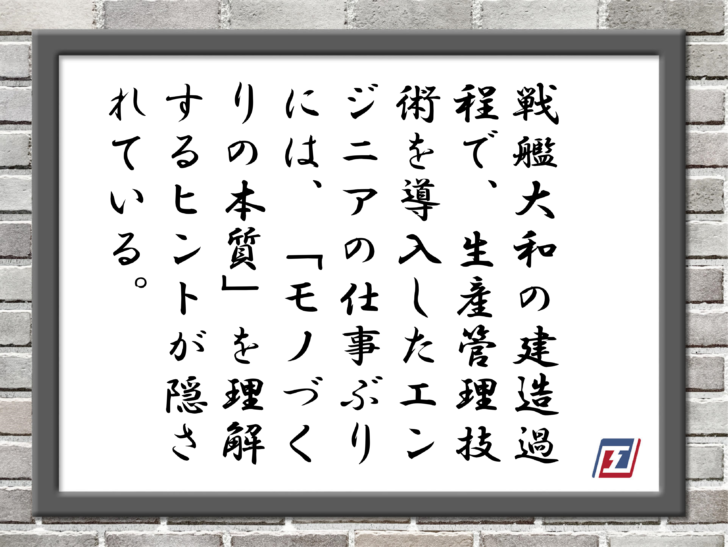
1.支援先の工場長と交わした「ゼロ戦」の会話
弊社が支援先で種々の指導をする中で、心に残る会話と出会うときがあります。
数年前の人時生産性向上プロジェクトでのこと。プロジェクトリーダーを務める30代後半若手工場長との打ち合わせの合間での一コマです。
「先生、ゼロ戦ってすごいですよね」
その工場長は、40人規模の板金加工現場を統括し、卓越したスキルとリーダーシップで現場を牽引する人材です。その工場長の祖父はモノづくりで商売をしていました。幼少期から切削加工や板金加工を身近に感じる環境で育ったのです。
その工場長がモノづくりに興味を抱くようになったのは、その祖父からモノづくりのDNAを受け継いだからでしょう。そして、仕事場として製造業を選び、中小製造業の最前線で奮闘するに至りました。
モノづくりに情熱を注ぐ人々は、往々にして乗り物にも深い関心を持ちます。その工場長もその例外ではなく、自動車から航空機まで、様々な「動くもの」への関心が高かったようです。
「どんなところがすごいと感じるのですか?」と私が尋ねると、彼の目が輝きました。
「今から90年も前の日本で、あれだけの性能が高い飛行機を設計して、大量に製造したことはすごいと思いませんか?」
ゼロ戦とは、日中戦争から太平洋戦争にかけて戦場で活躍した大日本帝国海軍の艦上戦闘機のことです。正式名称は零式艦上戦闘機。宮崎駿監督のジブリ作品「風立ちぬ」では、ゼロ戦の設計者である堀越二郎がモデルとなっています。
その工場長の話は、ゼロ戦を戦争の道具としてではなく、「究極の工業製品」として捉え、その設計・開発および製造のプロセスがスゴイと感じたというものです。
現代の中小製造企業が直面する「品質」と「コスト」と「納期」のバランスという永遠の課題は、90年前の日本の製造現場でも存在していました。モノづくりの本質は今も昔も変わりません。
当時の関係者は、デジタルツールが無くても、ゼロ戦を設計・開発し、限られた技術と資源の中で製造をしながら、革新的な解決策を見出してきたのです。
工場長との会話を通じて、製造業における「モノづくりの本質」と「デジタル化」の融合がいかに重要かを再認識しました。中小製造企業が生き残るためには、この二つの要素をバランス良く発展させる必要があります。
デジタルトランスフォーメーション(DX)が叫ばれる現代においても、根底にある「モノづくりの本質」を忘れてはならないと強く感じます。
重要なのは「モノづくりの本質」の方なのです。
2.戦艦大和から見えてくるモノづくりの本質
「ゼロ戦」が出てくれば、自然と「戦艦大和」が浮かびます。
90年前の日本が持っていた技術力の集大成とも言えるこの巨大戦艦の製造プロセスには、中小製造業経営者が、「モノづくりの本質」について、改めて学ぶ点も多いのではないでしょうか。
戦艦大和は、全長約260メートル、幅約40メートルという巨大な船体に、世界最大の46センチ主砲3基9門を搭載した超弩級戦艦です。呉海軍工廠で建造され、1941年(昭和16年)に就役しました。7万トンを超える排水量は、当時の世界最大を誇っていたのです。
超弩級戦艦という表現から、その巨大さは「鉄の塊!!」という印象だったに違いありません。
現代のように3Dモデリングやプロジェクト管理ソフトなどのデジタルツールが存在しない90年前、こうした空前絶後の巨大プロジェクトをどのように管理し、どのように「鉄の塊!!」の製造工程を最適化したのか?
そのプロセスに強い関心を持ちました。多くの中小製造企業経営者も同じではないでしょうか?
この疑問に答えてくれた書籍があります。
「戦艦大和誕生」(前間孝則著)
前間氏はジェットエンジン設計のバックグラウンドを持つノンフィクション作家です。エンジニアの視点による緻密な取材に基づいて書かれた内容には、モノづくりの本質を改めて考えるヒントにあふれていました。
特に興味深かったのは、この巨大プロジェクトを率いた西島亮二海軍技術大佐の存在です。
西島技術大佐は、単なる管理者ではなく、革新的な生産技術と徹底した生産管理システムを導入した先駆者でした。西島技術大佐とチームが実践した手法は、現代の生産管理を先駆けていたと言えます。
弊社が支援している中小製造企業の多くは、「人時生産性の向上」という課題に直面しています。慢性的な人手不足、国際競争の激化、デジタル化の波など、様々な課題が押し寄せる中、いかにして限られたリソースで最大の効果を生み出すか?
その答えの一部は、意外にも、90年前の戦艦大和建造プロジェクトにもあると感じたのです。生成を高める要点は「デジタル化」ではなく「モノづくりの本質」の方にあります。
西島技術大佐が実践した方法は、現代の中小製造企業にも直接応用できる普遍的な原則を含んでいます。IoTやAIが話題となる現代においても、製造業の根幹をなすのは、「モノづくりの本質」に基づいた「基本の徹底」です。
戦艦大和は悲劇的な最期を迎えましたが、その建造過程で見られた、日本のモノづくり精神と技術革新の様は、中小製造企業の未来へ向けたヒントを与えてくれます。
温故知新です。
記述の出典は全て、前間孝則氏の著書「戦艦大和誕生」です。
3.戦艦大和の製造プロセスにおける革新性
戦艦大和は、全長約260メートル、幅約40メートル、排水量約7万トンという巨大な船体に、46cm主砲3基9門を搭載した、当時世界最大の戦艦でした。しかし、その驚異的な点は規模だけではありません。戦艦大和の建造には、革新性があったのです。
大和型戦艦は1号艦「大和」と2号艦「武蔵」が、同時期に建造されました。両者は同じ図面から、それぞれ1号艦、2号艦として建造されたのです。同時に、超弩級戦艦を2艦も建造したことに、まずは驚きます。
製造過程を「大和」と「武蔵」で比べたのが下記です。
比較したのは、6項目です。
1.名称
2.建造場所
3.起工日
4.竣工日
5.工期
6.船体(船殻)建造総工数
戦艦は、水に浮かんでいる部分や甲板、大砲や艦橋部、さらには中に設置される動力や船室などで構成されています。6項目目の「船体(船殻)建造総工数」とは、水に浮かんでいる部分の建造に要した工数のことです。工数は人数と作業時間をかけた数値です。
1.名称
戦艦大和 :A140一号艦
戦艦武蔵 :A140二号艦
2.建造場所
戦艦大和 :呉海軍工廠
戦艦武蔵 :三菱重工業長崎造船所
3.起工
戦艦大和 :1937年(昭和12年)11月04日
戦艦武蔵 :1938年(昭和13年)03月29日
4.就役
戦艦大和 :1941年(昭和16年)12月16日
戦艦武蔵 :1942年(昭和17年)08月05日
5.工期
戦艦大和 :4年1か月
戦艦武蔵 :4年4カ月
6.船体(船殻)建造総工数
戦艦大和 :約●●●工数
戦艦武蔵 :約200万工数
最後の項目、船体(船殻)建造総工数で、大和のそれをあえて伏せています。
戦艦武蔵は約200万工数でした。では、大和のそれはどれくらいだったか?
工期を見ればほぼ同じです。大きく異なるのは建造場所くらいです。そうであるなら、若干の差はあるものの、戦艦大和でも、200万工数くらいだっただろうと考えるのが、普通ではないでしょうか。
で実績は・・・・・。
6.船体(船殻)建造総工数
戦艦大和 :約100万工数
戦艦武蔵 :約200万工数
1号艦「大和」の船体(船殻)建造に要した総工数は2号艦「武蔵」の半分だったのです。
前間氏の記述では、下記のように表現されています。
・西島が採用した建造方式がいかに革新的であったかを示す事実がある。「大和」の船体(船殻)建造に要した総工数が、三菱重工業長崎造船所が担当した二号艦の「武蔵」のほぼ二分の一だったことだ。(上巻p14)
・(大和の)船殻工場関係の工事を1,474,000工数と予定した。それが実際には999,000工数にまで低下している。すなわち予定の68%で完成したことになる。(下巻p78)
呉海軍工廠で建造された大和の船体(船殻)建造総工数は、三菱重工業長崎造船所が担当した武蔵のほぼ2分の1で済んだのです。同じ図面から建造されたにもかかわらず、なぜこれほどの差が生まれたのか?
両者の建造方式の違いが、決定的だったのです。
この工数の差では、両者の建造予算の違いが、あまりに巨額になるため、海軍内で大問題となりました。当時、このことは、極秘にされていたようです。
「武蔵」を建造した三菱長崎の建造方法に欠陥や手違いがあったわけではありません。三菱長崎は数ある民間造船所の中でも最高の技術を誇っていたのです。彼らは彼らで、従来通りの方式で、必死に建造を進めていました。
したがって、差を生み出したのは、西島技術大佐が率いる呉工廠の革新的な建造方式だったと言えます。
優秀な技術者や工員、関係者が一丸となって取り組んだ結果、画期的な効率化を実現したのです。建造設備や地理的条件などの違いはあったものの、これほどまでの差が生まれたことは、海軍の造船関係者にとっても大きな驚きでした。
この事例は、従来の仕事のやり方を革新的に変えることで、大幅なコスト削減と効率化が可能になることを示しています。
中小製造企業の経営者にとって、「当たり前」と思われている考え方や仕事のやり方を見直す重要性を教えてくれる歴史的事例と言えるのではないでしょうか?
また、西島技術大佐のリーダーシップが改革を後押しました。改革には、トップの強力なリーダーシップが不可欠であることも教えてくれています。
4.戦艦大和の生産管理
では、呉工廠は、どのような革新的な建造方式と生産管理で、これほどの効率化を実現したのか?現代の中小製造業にも通じる重要なポイントがここにあります。
第一に挙げられるのが「ブロック建造法」と「先行艤装(ぎそう)」の採用です。
従来の船体建造は船台上で骨組みから順に組み上げていく方式でした。呉工廠では船体を複数のブロックに分け、それぞれを並行して製作する新たなやり方を採用したのです。
さらに、各ブロックに艤装品(配管や電気系統など)をあらかじめ取り付ける「先行艤装」を実施しました。現代の「モジュール生産」の先駆けとも言えます。
これにより作業空間の制約が減少し、効率が飛躍的に向上したのです。これらは、現在の造船技術では当たり前の技術になっています。
戦艦大和より前に建造した艦船でトライアンドエラーしながらこれらの技術を培っていったのです。そして、満を持して戦艦大和建造時に、大規模かつ組織的に採用し、従来の建造法から完全に脱却しました。
トップ層の強力なリーダーシップがなければ成し遂げられません。
私達は、西島技術大佐をはじめ、多くのエンジニアによって発揮された強いリーダーシップを学びたいのです。
第二に、「リベット(鋲接)工法」から「電気溶接法」への移行です。
当時、船体の接合は主にリベットを打ち込む方式が主流でしたが、呉工廠では積極的に電気溶接を採用。溶接は作業時間の短縮だけでなく、船体の軽量化や強度向上にも寄与し、一石二鳥の効果をもたらしました。新技術への果敢な挑戦も成功の鍵となったのです。
しかし、こうした革新的な建造法を支えたのは、徹底した「生産管理」の仕組みでした。前間氏の記述の中、注目したのは、以下の3点です。
まず「工数管理の徹底」です。
次に「材料や部品の標準化」
そして「作業の標準化」です。
その管理手法自体に驚きはありません。多くの中小製造企業経営者もご存じのように、今では当たり前になっているからです。
注目したいのは、その管理手法を導入した背景や導入したときの状況です。
今から90年前の現場を頭に浮かべてください。
現場には、科学的な考えを理解する土壌は全くありません。職人気質の作業者ばかりです。さらには、エクセルもなければ、スケジューラーなど、現在、普通に活用されているデジタルツールは、全くなかったのです。
そうした環境で、生産管理を導入していったエンジニアの仕事ぶりは、「モノづくりの本質」を深く理解するのに役立つと、強く感じます。
戦艦大和の製造プロセスの土台となった「日本のものづくりDNA」を紐解くことで、中小製造企業の未来の競争力を高めるヒントが見つかるかもしれません。
特に、呉海軍工廠で建造された大和の船体(船殻)建造総工数は、三菱重工業長崎造船所が担当した武蔵のほぼ2分の1で済んだ、という事実に注目したいです。
当時の革新的要素技術と新たな管理技術の相乗効果による成果と言えます。
導入された要素技術も管理技術も、今では当たり前です。我々は、さらにデジタルツールも活用して、当時と比べれば、数倍、数十倍の高度化、効率化を実現しています。
導入された要素技術や管理技術に真新しさはありません。したがって、多くの中小製造企業経営者がそれ自体から学ぶものはないでしょう。
今では当たり前の技術ばかりだからです。
学び、知りたいのは、それらを導入したリーダーたちの言動です。リーダーシップ発揮の様子に注目したくなります。
エベレストを世界で初めて登頂した人は偉大です。現在と比べれば、機能に制約のある装備で達成しています。なんでも、ゼロイチはすごいです。
西島技術大佐をはじめ、多くのエンジニアによって発揮された強いリーダーシップの様子を知りたくなります。
そこで、引き続き、管理技術の方に焦点を当てることにしました。
「工数管理の徹底」
「材料や部品の標準化」
「作業の標準化」
これら3項目を取り上げます。西島技術大佐をはじめ多くのエンジニアによって発揮された強いリーダーシップの様子から「モノづくりの本質」を考えたいのです。
弊社は、人時生産性を高める観点で、中小製造企業経営者の支援をしています。モノづくりの本質を深く理解できれば、人時生産性を高める要点にも気付くはずです。
記述の出典は全て、前間孝則氏の著書「戦艦大和誕生」です。