戦略的工場経営ブログ危機管理
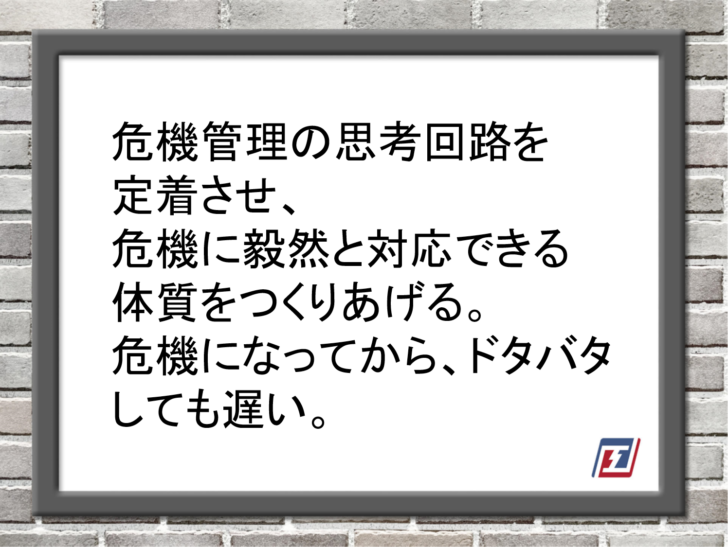
「未然に防ぐ」工場経営を目指していますか?
1.これから5年先、10年先の見通し
現在は過去の結果であることを踏まえれば、将来は現在の結果です。したがって、豊かな将来を目指すなら、”今”、やるしかありません。今、やるべきことの判断基準は、5年先、10年先の見通しです。
「従来からの仕事のやり方を変えずに継続したら、今の事業はどうなるか?」と自問してください。
ここで、バラ色の将来だけが浮かんでくるなら問題はありません。このまま全力で突っ走りましょう。
だた、こうした企業はまれでしょうし、そもそも、将来にバラ色の見通ししか浮かばなければ、「経営者として失格!」との謗りを免れないかもしれません。
変化の時代です。不測時の事態にも直面します。現状の延長線上に夢だけを描いていては、変化に対応できず、”その時”には、あたふたするしかないでしょう。
誰でも「自分は大丈夫」と思い込みがちです。正常性バイアスを忘れてはなりません。
2.危機感の共有
先日の個別相談で、ある電子部品メーカーの経営者は、下記のように言い切っていました。
「5年間は持たないです。」
先の質問を投げかけたとき、即答されました。
その経営者が言う、持たないとは、事業が立ち行かなくなるということです。危機感を全社で共有して、儲かる工場経営を目指した全社活動に着手しなければ明日はないとの覚悟を示されました。
また、ある紙媒体加工業の経営幹部は、今は収益上の問題はないけれども、5年先、10年先を考えると、現在の事業規模を維持できなくなると語っていました。同じ”紙”でも、宅配や運搬で使われる段ボール箱向けの”紙”なら、今後も需要は伸びそうです。
しかし、メディアとしての”紙”は、電子書籍拡大などによる紙媒体の需要減のあおりを受けて、売上は右肩下がりになると幹部は予想しています。したがって、その幹部も、仕事のやり方を変えなければならないと考えました。
豊かな現場を目指した、儲かる工場経営とは、現場改革や意識改革、構造改革を、たえず、たゆまず、実行していくことです。
変えるために、経営者や経営幹部が先頭に立ちます。全社を一体化して、ベクトルを揃えることが欠かせません。
生産性ロードマップをまとめるにあたって、考えるべきは、「従来からの仕事のやり方を変えずに継続したら、今の事業はどうなるか?」です。すでに起こっている将来のできごとと将来起こるであろうできごとを設定します。
経営者層の多くは、先のお二人のように、「このままではまずい」と考えるのではないでしょうか。改革のきっかけは危機感の共有です。「健全」な危機感は活動の原動力になります。
3.「未然に防ぐ」、「事を起こさない」、「先手必勝!」
健全な危機感を現場と共有して、「事を起こさない」あるいは、「事が起こってもダメージを最小化する」工場経営を目指します。
中小製造現場は少数精鋭です。トラブルが起きてから、都度、モグラ叩きをしているようでは、疲弊します。
中小の儲かる工場経営の要諦は、「未然に防ぐ」、「事を起こさない」、「先手を打つ」にもあるのです。そこで、5年先、10年先を見通しながら「儲かる工場経営」を実践したいとお考えの経営者の方々に持っていただきたい思考回路があります。
「危機管理」の思考回路です。
「ウチはリスクマネジメントをやっていますよ。」
「BCPを毎年、見直していますから、そうした考え方が定着しています。」
との声が皆さんから上がってくるかもしれません。
起こりうるリスクを全て洗い出し、適切に対応するための活動を管理する重要性は、従来も、今後も変わらないところです。BCPや保険に代表されるリスク管理が不要になることはないでしょう。
ただ、ここでお伝えしたいのは、こうしたリスク管理ではなく、危機管理なのです。
4.リスク管理と危機管理
リスク管理と危機管理、これらの違いがお分かりになるでしょうか?
クライシスマネジメントコンサルティングの第一人者である林祐氏の著書「事業大躍進に挑む経営者のための”クライシスマネジメント”」にわかりやすい説明があります。
(なお、同著はリスク管理と危機管理の違いを、見事に、わかりやすく解説しており、新たな観点を与えてくれる良書です。伊藤は目から鱗が落ちました。)
林氏は、危機(クライシス)を機会に転じて、事業を躍進させる危機管理の重要性、有用性を説いています。リスク管理と危機管理は、狙いが、明らかに異なるようです。
「リスクマネジメントは、あらかじめリスクを評価し、そのリスクが現実になったときに備える対策を講じておくことが課題だ。(中略)この対策を講じたからと言って危機そのものを避けることはできないし、想定外の問題に対応できない。
(中略)一方のクライシスマネジメントは、そもそも危機に陥りにくい体質をつくり、想定外の危機に際しては、毅然と対応する自信を経営者に与え、その危機を機会に転じていこうとするマネジメントであり、・・」
(出典:林祐著、事業大躍進に挑む経営者のための”クライシスマネジメント”)
この考え方は、儲かる工場経営でも大いに生かせます。たとえば、品質原価という考え方がそうです。
品質コストを構成する「評価・予防コスト」と「失敗コスト」はトレードオフであり、失敗コストを最小化するために、評価・予防コストに注目します。
「未然に防ぐ」、「事を起こさない」、「先手必勝!」です。
危機管理の重要性を説く林氏の考えに、伊藤も共感しています。
東日本大震災以降、「想定外」という表現を耳にすることが増えました。最もらしい表現ですが、責任者がこの表現を用いると、言い訳のようにしか聞こえません。上司からこうした説明を聞かされる部下は納得できるでしょうか?
モノづくりが複雑化、高度化しているなかで、今後は「想定外」が普通に起きることでしょう。技術進化に必要なイノベーションとはそのようなものです。「想定外」を避けていたら、新たな挑戦に挑めません。
「想定外」を言い訳にしない危機管理の思考回路を持ちたい所以です。
5.健全な危機感の醸成
「未然に防ぐ」、「事を起こさない」、「先手必勝!」の思考回路を現場と共有しつつ、想定外の危機に際して、毅然と対応できる体質をつくります。
生産性ロードマップをまとめるにあたって、考えるべきは、「従来からの仕事のやり方を変えずに継続したら、今の事業はどうなるか?」であると申し上げました。経営者が自問自答し、起こりうる危機を事前に設定するのです。
そもそも将来を予測することは不可能ですから、起こりうる危機を経営者が決めてしまいます。そうして、その危機をどのように乗り越えるか、時系列でやるべきことを明らかにするのです。
儲かる工場経営の危機管理では、起こりうる危機を設定し、その解決策を実践します。仮説と検証です。
設定した危機は、形を変えて来るかもしれません。それならば、解決策を修正して臨めばいいです。
また、設定した危機は、そもそも起こらないかもしれません。それは、それで、良かったとなります。
少なくとも、林氏が説くところの「そもそも危機に陥りにくい体質、毅然と対応できる体質」を目指すことになるのです。
儲かる工場経営とは「仮説と検証」の繰り返し(現場活動で日常的にやられていますよね)であり、危機管理もそうした論理的な思考の元で行われます。「仮説と検証」という論理的思考が抜けていては、不確実性が高まる荒波を乗り越えられません。
ここで取り上げる危機は、起こりうると設定されただけです。あくまで仮説、まだ起きていません。家屋からすでに火の手が上がっているわけではなく、そうした事態を回避するよう、防火に知恵を絞るようなものです。まだまだ、ゆとりがあります。
ですから、健全な危機感を醸成できるでしょう。健全な危機感の醸成は一体感へつながり、生産性ロードマップの推進を加速させます。
そうして、危機管理の思考回路を定着させ、想定外の危機に際して、毅然と対応できる体質をつくりあげるのです。
生産性ロードマップで健全な危機感を共有しませんか?