戦略的工場経営ブログ付加価値額生産性
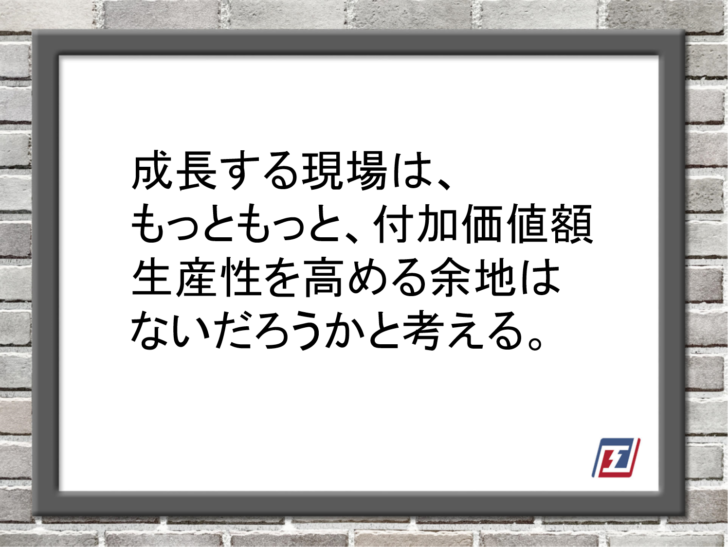
付加価値額生産性を高める余地はありませんか?
1.儲かる工場経営の観点
今年最後のブログでは、付加価値額生産性を取り上げます。
付加価値額を積み上げる。これが儲かる工場経営の観点です。積み上げるべきものは売上高ではありません。製造現場だけでなく営業部隊も同様です。
国内市場規模が右肩上がりで拡大していた頃、増加する売上高に利益が付いてきました。造れば売れる時代であるなら、売上高の積み上げにひたすら汗を流す仕事のやり方は間違っていません。機会損失の回避が利益の最大化につながるからです。
しかし、顧客要望も多様化し、国内市場規模の伸びが鈍化している昨今、同じ仕事のやり方では生き残れないでしょう。経営者の号令一下、全社一丸となって付加価値額の積み上げに全力投球できている工場が儲かります。
儲かる工場経営の肝は将来投資でもある固定費を効率良く回収することに他ならないからです。
固定費の大部分が従業員の給料であり、これには昇給分も含んでいます。モノづくり事業で儲けるために経営者が将来を見通して現場へ計画的に投じる資金、投資のような性質を持っているのが固定費です。
固定費こそが儲かる工場経営の原動力であり、投じた資金は効率良く回収し続ける必要があります。
これがいわゆるゴーイングコンサーンの前提条件です。したがって、この固定費を回収するパワーの源となる付加価値額に注目しなければなりません。付加価値額で固定費を回収する以上、積み上げるべきものは売上高ではなく、付加価値額なのです
2.付加価値額生産性
製造業に限らず、あらゆる業種が人手不足の問題に直面していると言われています。そして、新卒の採用はそのほとんどが大企業向けとなり、中小現場での新卒の採用が難しくなるであろうことは容易に想像できます。
少子化という現実を目の前にして、現場へ投じられる人的資源が大きく制約されるであろうことは火を見るよりも明らかです。ですから、現場へ投入できる人的経営資源に限りがあるなかで、いかに効率良く付加価値額を積み上げるかが、中小製造現場、生き残りの論点となります。
弊社がご指導の中で付加価値額生産性を重視するのにはこうした理由があります。
働き方改革が叫ばれている昨今、インプットとなる工数は時間単位で管理することも求められるでしょう。この付加価値額生産性をひたすら高め続けることです。これは儲かる体質の事業や現場を手にすることに繋がります。損益分岐点比率を引き下げることに寄与するからです。
儲かる工場経営の現場力は付加価値額生産性で計ります。
3.労働生産性の国際比較 2018
先日、(公財)日本生産性本部が「労働生産性の国際比較 2018」を発表しました。弊社が注目している発表のひとつであり、特に下記2つが目を引きました。ちなみに、労働生産性は一般的に分母は従業員数、分子は付加価値額で定義され、ここで言う付加価値額生産性と同じような概念です。
1.日本の時間当たり労働生産性(2017年)は47.5ドルで、OECD加盟36カ国中20位。
2. 日本の製造業の労働生産性(2016年)は99,215ドルで、OECDに加盟する主要31カ国中15位。
日本の時間当たり労働生産性は、主要先進7カ国でみると、データが取得可能な1970年以降、最下位が続いています。米国(72.0ドル/7,169円)の3分の2程度です。
また、日本の製造業の労働生産性は、1995年及び2000年、主要国のなかでトップでしたが、その後、2000年代に入ると大きく後退し、2016年には15位にまで落ち込んでいます。
グローバルにみると日本の生産性は低い水準にあると報道等でしばしば指摘されますが、よりどころが日本生産性本部が発表するこれらのデータです。
・日本の時間当たり労働生産性が1970年以降、主要先進7カ国でワーストを継続している事実があること。
・国内でも生産性が高いと言われている製造業であっても、2000年以降、順位を落としている事実があること。
これらの事実を改めて考えたいです。
4.付加価値額生産性を高める余地は何だろうか?と考える
日本の製造業はトヨタ生産性方式をはじめ、「カイゼン」など、世界が注目するモノづくりのやり方を生み出してきました。製造現場には、自ら主体的に取り組む”現場活動”で成果を出してきた自負があります。
したがって、主要先進7カ国で日本の生産性は50年ほど前から最下位が続いているとか、製造業もここ20年の間でドンドン、生産性の順位を下げているとか言われてもピンとこないかもしれません。
付加価値算出のやり方がおかしいのでは?、為替レートが影響しているので本来の実力値を表してはいないのでは?という声も上がってきそうです。
製造現場でチーム力を生かして日々頑張っているリーダーや作業者の仕事ぶりを肌感覚で理解している方なら同様な疑問が沸き上がってくるのではないでしょうか?
ウチの現場ではやることがないくらい改善活動をやり切っていると考える経営者ならなおさらでしょう。しかしながら、さらなる成長や発展を目指すなら、こうした数値をしっかり受け止め、貴社にも当てはめて考えてみたいです。
もっともっと、付加価値額生産性を高める余地はないだろうか?
儲かる工場経営を目指したモノづくり事業を進めていくうえで、あらゆる活動が、国内だけで完結していることは稀です。中小製造現場へ投入する経営資源にしろ、産出される成果物にしろ、全ては”世界”と結びついています。
製品の納入先は国内向けのみかもしれませんが、最終製品の市場は海外であることは多々あることです。また原材料価格が世界の相場で決められることも自明の理であり、さらには外国人労働者を活用することもあります。
ですから、生産性を世界と比べることは、儲かる工場経営を目指すうえでも欠かせないことです。
少なくとも製造業の労働生産性が2000年頃までは世界のトップクラスであった事実があります。それがここ20年で順位を下げてきたのには、やはり何らかの”変化”があり、その”変化”に日本のモノづくりが追い付いていないと考えたいのです。
国内製造業の労働生産性自体は増加傾向を維持しています。その一方で世界と比べて順位が落ちているということは、世界の伸びが目覚ましいということです
すでにやりつくしていると考える経営者はより高みを目指し、解決すべき問題がまだまだあると考える経営者はまずは現場改革を目指し、もっともっと、付加価値額生産性を高める余地は何だろうか?と考えてください。
製造業企業数の99%が中小製造企業であり、製造業従業者数の66%が中小製造企業従業者です。
国内モノづくりの土台をなしている中小製造業界の生産性向上が製造業全体の生産性を押し上げ、さらに、こうした効果が他の業界へも波及して、それが最終的には日本の労働生産性を高めることにつながります。
ぜひ、改めて、ご自身の現場を眺め、もっともっと、付加価値額生産性を高める余地は何だろうか?と考えてください。来年も引き続き、多くの中小製造企業の経営者の方々と生産性を高める活動を強力に推進して参ります。
・成長する現場は、もっともっと、付加価値額生産性を高める余地は何だろうか?と考える。
・現状維持にとどまり、今の仕事のやり方でいいと思い込んでいる現場は、我々に問題はないと考える。
付加価値額生産性を高める仕組みづくりに着手しませんか?