戦略的工場経営ブログ儲かる工場経営を計測する
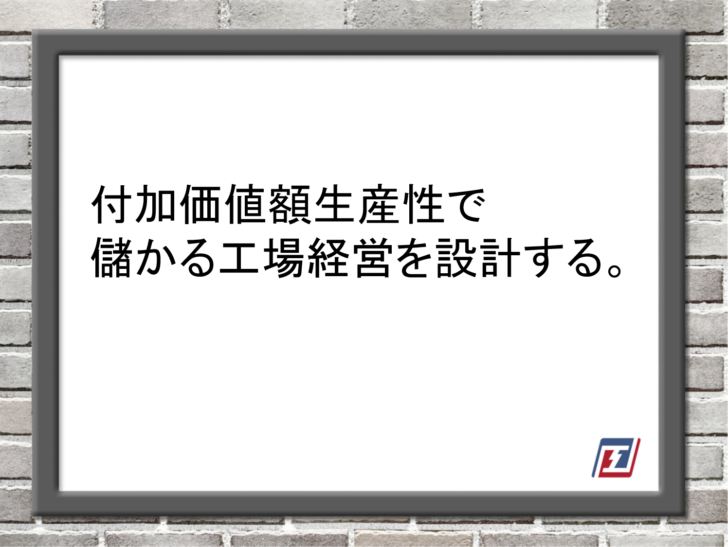
儲かる工場経営を計測できますか?
1.現場リーダーにも理解してもらいたい生産性
今後、5年先、10年先を見通すロードマップを描くときに欠かせない指標があります。
生産性です。
それはわかっているし、耳にタコができるほど聞いているよという言葉が経営者や経営幹部の皆さんから返ってきそうですが、ほんとうにそうでしょうか?
生産性の考え方を儲かる工場経営へ生かしている現場は少ないと感じています。納期を判断基準として、指示された製品を納期通り製造すれば問題がないと考えている(思い込んでいる)現場リーダーも多いのではないでしょうか?
納期遵守は商売の基本ですから、納期を重視する姿勢はこれからも欠かせません。ただ、儲かる工場経営を継続したいのなら、これでは行き詰まります。下請け型の事業であるならなおさらです。
納期に間に合わせる仕事のやり方をやってさえすれば問題のない時代は過ぎつつあります。高度成長期にある新興国ならいざ知らず、国内において、そういった段階をとうの昔に卒業していることはご存じの通りです。モノを造っていれば儲かる・・という時代ではありません。
商売を成長路線へ乗せるのに必要なのは1)既存顧客の囲い込み、2)新規顧客の開拓の2つですが、そのために欠かせない論点として、”顧客満足度向上”だけでは、もはや不十分だとも言われています。
いわゆるQCDを満たすことは、もはや当たり前です。顧客はそれだけの理由でみなさんの会社を選んでくれない時代へ移行しつつあるとも言われています。
満足に加えて必要なのは「感動」・・・、こんなことも言われるようになってきたのです。顧客の要望が変化しているのに、相変わらず内部事情を優先させた仕事のやり方をしていてはゆくゆくどうなるか?言うまでもありません。
外部環境が刻々と変化しているのに、現場では”納期さえ・・・”という考え方に留まり、自分は変わる必要がないと信じているようでは、当然のように現場改革は進みません。
プロジェクトチームを組むこと自体が不可能です。今後、直面する外部環境変化へ対応しようと知恵を絞っている経営者や経営幹部とのベクトル合わせの際にずれが生じます。
ですから、納期基準に染まっている現場リーダーの思考回路に少々、手を入れる必要があるのです。
5年先、10年先を見通したとき、経営者の頭に浮かぶことのひとつに「人手確保」があります。少子化を背景として、今後20年で生産年齢人口が20%減るとの予想がなされている以上、人手不足へ手を打つことは中小現場の喫緊の課題です。
人手を確保する手立てとして、外国人労働者や高年齢労働者の活用が考えられます。
最近、政府は継続雇用年齢を65歳以上に引き上げる法改正に向けて、企業に対して70歳までの雇用を促すための計画の策定を義務付けることを検討しているとの報道がありました。
現場は助かるとの声が上がっている一方で、若手の雇用の場を奪う、若手の賃金上昇の障害となるなどの指摘も出ているようです。
外国人労働者の活用についても今後、いろいろな議論がなされると思われます。
いずれにせよ、賛否両論、 諸説紛紛、喧々諤々、議論百出・・・というように統一した見解が示されるにはかなりの時間がかかりそうです。
それに、そもそも、外国人労働者や高年齢労働者の活用が解決手段になり得るか否かは現場の事情で異なります。
みなさんの現場でも、これらが根本解決策になるのかどうかは、やってみないとわからないというのが正直なところではないでしょうか?
やってみなければわからないことは、経営者の号令一下、挑戦してみればいいわけで、ダメならやり直せばいいのですが、やってみないとわからない手段に頼るだけでは心許ないです。
そこで、企業規模の大小に関係なく、自助努力で成果につながる手段に注目するべきであり、それが生産性を高める活動、生産性向上活動です。
生産性は分母と分子の2つの数字から構成されます。分母が「投入量」、分子が「産出量」であり、これら2つの数字の組み合わせで評価できるところに生産性の”妙味”があるのです。
人手不足とは、分母の「投入量」を減らさざるを得ない状況に直面することと言い換えられ、分子の「産出量」をどのようにコントロールするかが課題となってきます。
分子を減らしつつ、分母の減少を最小限にとどめるのか、従来を維持するのか、逆に増加させるのか・・・。これは経営者が意思決定する戦略次第です。
分母と分子を対比させた思考が求められ、従来の「産出量」だけに焦点を当てていた仕事のやり方だけでは、先を見通した戦略は考えられません。
経営者にとって、生産性の考え方が欠かせなくなるのは火を見るよりも明らかなことであり、経営者の右腕役となる現場リーダーも考え方を理解し、使えるようになる必要があります。
セミナーや現場でのご指導の場でお話ししていることですが、現場改革での生産性向上は3段階あり、第1段階目は多くの場合、”ムダ取り”です。
そこから多様な活動に展開して、最終的に儲かる工場経営へ結びつけるわけですが、この第1~第2段階目の活動は現場独自です。業種業態、規模で異なります。
しかし、第3段階目で目指す生産性向上は、全ての中小現場で共通していることです。経営者の右腕役となる現場リーダーにはしっかりと理解してもらいたい生産性向上であり、経営者はそのことを教える必要があります。
その生産性とはなにか?
それは・・・。
2.付加価値額生産性
儲かる工場経営での生産性向上は3段階あり、そのうち、1段階目と2段階目は弊社で言うところのタイプXとタイプY生産性向上の組み合わせとなり、これは現場の状況に応じて方針が異なります。
しかし、次の3段階目の生産性向上はあらゆる中小現場に共通です。
それが、付加価値額生産性です。
分母は人、あるいは工数(人時、人日など)、分子は付加価値額となります。
これは労働生産性とも表現され、国内の労働生産性が欧米諸国のそれよりも低いことが問題視されているのは周知の事実です。
日本生産性本部「日本の生産性の動向2017年版」によると2016年時点で日本の労働生産性は21位です。
1位 アイルランド 168,724US$
2位 ルクセンブルク 144,273US$
3位 米国 122,986US$
4位 ノルウェー 117,792US$
5位 スイス 115,900US$
8位 フランス 104,347US$
10位 イタリア 102,107US$
14位 ドイツ 97,927US$
18位 英国 88,427US$
21位 日本 81,777US$
日本が欧米主要国の後塵を拝していることがわかります。また、一般的に勤勉な国民性で知られるドイツも世界のトップ10に入っていないことも興味深いです。
いずれにせよ、国内では働き方改革が声高に叫ばれていますが、国力アップの観点からも、あらゆる業種の関係者が付加価値額を効率よく高めることに挑戦すべき状況であると言えるでしょう。
私たち中小の製造現場でも同様であり、高めたいのが、まさに、この付加価値額生産性です。
従来対比で人手が不足しようとしまいと、この数字は少なとも死守維持しなければならない数字であって、豊かな成長を目指すなら向上させ続けないとならない数字となります。
付加価値額は現場の給料に直結する数字そのもですから、その生産性が低下すると「ない袖は振れぬ」状態になりかねません。
ですから、これから付加価値額生産性にこだわりたいのです。
地域の中で、あるいは業界の中で少しでも高い給料を現場へ払ってあげたいと考える経営者の外せない経営指標でもあります。
5年先、10年先を見通し、将来へ向けて、他よりも、少しでもいい給料を現場へ払いたいのなら、生産性、特に付加価値額生産性の向上につながる継続的な現場活動が欠かせません。
人手が減ろうが増えようが、この数字は維持、成長させたいのです。
分母が減ったことを言い訳にして分子の付加価値額も減らし生産性を低下させることが、結果として何につながるのかを理解させ、そうならない施策を事前に打っていきます。
3.儲かる工場経営を計測する
成功へのストーリーをロードマップで描いて現場と共有し、現場のベクトルをそろえることが、現場改革の初手です。ですから、リーダーシップを発揮すべき現場リーダーには付加価値額生産性にこだわる意義を理解していて欲しいのです。
さて、現場活動では、現在の立ち位置を知ることからです。立ち位置を知るのに大手と中小の付加価値額生産性をくらべます。
2018年版中小企業白書には製造業の大企業と中小企業の従業員一人当たり付加価値額(労働生産性)推移が掲載されています。
財務省「法人企業統計調査年報」から作成したもので、ここでいう大企業とは資本金10億円以上、中小企業とは資本金1億円未満の企業のことです。
ちなみに、この資料での付加価値額の定義は下記です。
付加価値額=営業利益-支払利息+役員給与・賞与+従業員給与・賞与+福利厚生費+支払利息等+動産・不動産賃借料+租税公課
2008年秋に起きたリーマンショック以降のデータとして、2009年と2016年の2時点の推移を下記に示します。
〇製造業 大企業 付加価値額生産性
2009年 999万円
2016年 1,320万円
〇製造業 中小企業 付加価値額生産性
2009年 501万円
2016年 549万円
これら4つの数字をご覧になっていかがでしょうか?みなさんの現場で描いている付加価値額の規模感と一致しますか?
4つの数字から2つのことが事実として浮かび上がります。
(1)7年間で大手は32%UPしているのに対し、中小は10%UPにとどまっている。
(2)中小は大手の42%の付加価値額生産性にとどまっている。
従業員が1年間に生み出す付加価値額は大手と中小で差が拡大しています。2016年時点で中小は大手の半分以下です。
さらに、ここで労働分配率を大手と中小で下記とします。
大手 43.9%(出典:財務省法人企業統計調査17年10~12月期大企業)
中小 70.5%(出典:中小企業白書2018年版2016年度中小製造業)
そして、労務費・人件費=付加価値額×労働分配率で評価できるので、計算すると結果は下記です。
製造業 大企業 労務費・人件費
1,320×43.9=579万円
製造業 中小企業 労務費・人件費
549×70.5% =387万円
従業員への還元を増やそうと、労働分配率を70%と大手より30ポイント近く高めても、従業に支払える給料は大手の6割前後に止まっています。従業員へ少しでも多くの給料を払いたくても「ない袖は振れない」状況に中小製造企業は置かれているのです。
一般的に景気回復局面では、付加価値額アップが先行し、それに追随するように賃金が上昇すると言われているので労働分配率は低下傾向にあると言われています。
今は景気回復局面にあるのか否か?どちらの状況にあるにせよ、大手と中小の置かれた状況の違いは労働分配率の数値を見ても明らかです。
ですから、付加価値額の積み上げを図り、付加価値額の絶対値を拡大させることが成長路線で欠かせない論点となります。
そして、投入できる工数に制約がある将来を見据えると、”生産性を高めて”付加価値額の絶対値を増やす戦略の重要性に気付くのではないでしょうか?
だから付加価値額生産性なのです。儲かる工場経営を計測する指標とは、これ以外のなにものでもありません。
当ブログでしばしば取り上げるやる気を引き出す3つのポイントとは、自律性、有能性、大きな目的ですが、これらはいわゆる内発的動機付けによります。
仕事のやりがいや達成感が最高の報酬であるとする最近の動機付け理論に基づいた考え方です。
これと対比するのが外発的動機付けであり、いわゆる給料に代表される従来型の報酬のことで、これらを強調しすぎると、内発的動機付けに悪影響を及ぼすと理論では語られています。
ただ、現実には、そうでないと考えている経営者も多いのではないでしょうか?外発的動機付けにつながる要因で考えておかないことがあり、少なくとも”最低水準”に達成していないと、これはこれで問題です。
そういう観点からも、付加価値額生産性へ焦点を当てる意義があります。
付加価値額生産性を管理する仕組みをつくりませんか?