戦略的工場経営ブログ7つのムダに着目してムダ取りを仕組み化する
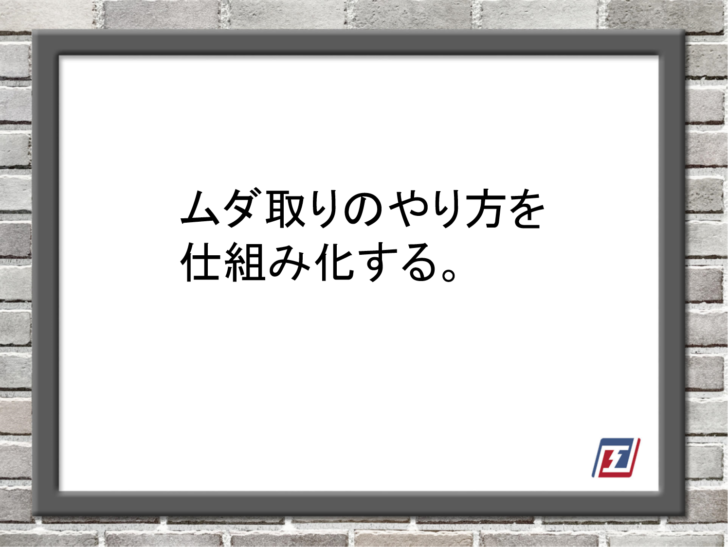
貴社の生産性向上活動は順調に進んでいますか?
1.現場のムダを見つけられるか?
儲かる工場経営の仕組み作りは、詰まるところ生産性向上の仕組み作りです。
中小製造現場における喫緊の課題は「生産性向上」だからです。
制約された経営資源を最大限生かさなければ生き残れません。
「生産性向上」に焦点を当てます。
さて、製造現場の役割は、
開発・設計部隊や営業部隊と連携して、
効率の良いモノづくりを実現させることです。
工場は製造現場だけでは成り立ちません。
価値を創り、
価値を造って、
価値を売る。
この3つの活動を通じて、お金を手にできことを全員で理解しなければなりません。
製造現場は、
価値を創るところは開発・設計部隊に、
売るところは営業部隊に任せるしかないのです。
したがって、経営者は連携の重要性を、現場へ伝える必要もあるのです。
その事実を認識したうえで、製造現場でやるべきことを考えます。
製造現場の仕事は、
工場全体として
効率の良いモノづくりを
実現させることであり、それが儲かる工場経営に繋がるのです。
全体最適化の視点です。
開発・設計部隊や営業部隊のことも
視野にいれた全体最適化の視点がないと、
現場からお金が生み出されないことに留意しなければなりません。
現場が部分最適化にとどまらないように経営者は現場を導く必要があります。
現場が全体最適化の主導権を握り、全体最適化の視点で生産性を高め続けるのです。
2.トヨタ生産方式の7つのムダ
セミナーやご支援の動で、
生産性向上の2つの観点を解説していますが、ポイントのひとつは「ムダ取り」です。
まずは、現場から徹底的にムダを取り除きます。
しかしながら、これが意外と難しいようです。
セミナーではたびたび、次のように尋ねます。
「現場のムダ取りをやり尽くして、ウチの現場にはムダはない、と言い切れる方はいますか?」
そもそも、
問題意識があるから
セミナーへ足を運んでいただいているので、
ここで挙手をする方はいないわけですが、
改めて現場の「ムダ」に
焦点を当てて欲しいのでこうした質問を投げかけるのです。
多くの現場では
なんとなくムダがあると感じています。
しかし、具体的には、
何がムダなのか明確に指摘できない・・・。
皆さんの現場でも、こうでないでしょうか?
ですから、
現場のムダを見つける方法を
手法として理解し、実践しやすくすることが有効です。
トヨタ生産方式で有名な
元トヨタ自動車副社長大野耐一氏が
その著書の中で説明していた
「7つのムダ」は有名です。
耳にしたことがある方も多いのではないでしょうか?
モノづくりの現場で
ムダを取りときの観点を
我々に与えてくれます。
7つのムダとは以下です。
(1)つくりすぎのムダ
(2)手待ちのムダ
(3)運搬のムダ
(4)加工そのもののムダ
(5)在庫のムダ
(6)動作のムダ
(7)不良をつくるムダ
これら7つは、
顕在化した現場のムダであり、
そうした観点で現場を眺めると、
ムダが見えてきます。
この顕在化したムダから、
潜在化したムダにまでさかのぼり、
ムダの原因を分析するのです。
この7つは記憶しておいて損はありません。
ただ、人間は忘れる動物であり、
耳にした情報の70%以上は
1日後忘れていると言われます。
短時間でいいので、
繰り返し復習することが
知識の定着に有効ですから、
現場巡視の度に、これらを思い出すのもいいやり方です。
ここでは、「何にムダがついているのか」に着目します。
記憶したいことを、意味づけして頭に定着させるのです。
7つのムダがついている対象は、
大きく、3つに分類できます。
一つ目は「生産の3要素」。
人、モノ、設備です。
二つ目は「工程分析4項目のうち価値を生まない2つの工程」。
つまり、運搬、停滞です。
三つ目は「しくみ、特に日程計画」。
受注生産形態における小日程計画です。
日程調整作業を現場に丸投げしていませんか?
7つのムダを、
それぞれ割り振ると、
次のようになります。
1.生産3要素(人、モノ、設備)についているムダ (2)(4)(6)(7)
(2)手待ちのムダ
(4)加工そのもののムダ
(6)動作のムダ
(7)不良をつくるムダ
2.価値を生まない工程(運搬、停滞)ついているムダ (3)(5)
(3)運搬のムダ
(5)在庫のムダ
3.しくみ、特に日程計画についているムダ (1)
(1)つくりすぎのムダ
3つめの(1)つくりすぎのムダについて若干、説明を追加します。
多くの中小製造現場は
受注生産形態であるので、
死蔵在庫を抱えるような
造りすぎという事態よりも、
慢性的に抱えている問題があります。
それは、小日程計画を
うまく使いこなしていない
(あるいはない)ために、
生産活動が適切に行われていないことです。
生産活動を支援する仕組みが不十分だということでもあります。
成り行き管理で納期調整を現場に丸投げしている状況に陥っている現場が少なくありません。
その結果、全体最適化の視点抜きに生産活動が進んでいきます。
不適切なしくみのため、
現場に「ムダ」な、余分な負荷(ストレス)かがかかっているのです。
3つめでは、死蔵在庫の懸念の解釈を広げて、適切でない生産活動も含めます。
7つのムダを3つに分類しました。
関連をイメージできれば、
7つのムダを頭に
思い浮かべられるのでは
ないでしょうか?
ムダをイメージできれば、
ムダを見つけやすくなります。
指名手配された犯人の顔写真が、
あるのと、無いのとでは、
検挙率は明らかに違うでしょう。
現場を巡視するときに、
7つのムダを思い浮かべて下さい。
ムダが見えてきます。
ムダ取りのやり方をしくみ化しませんか?