戦略的工場経営ブログ工程分割と工程統合
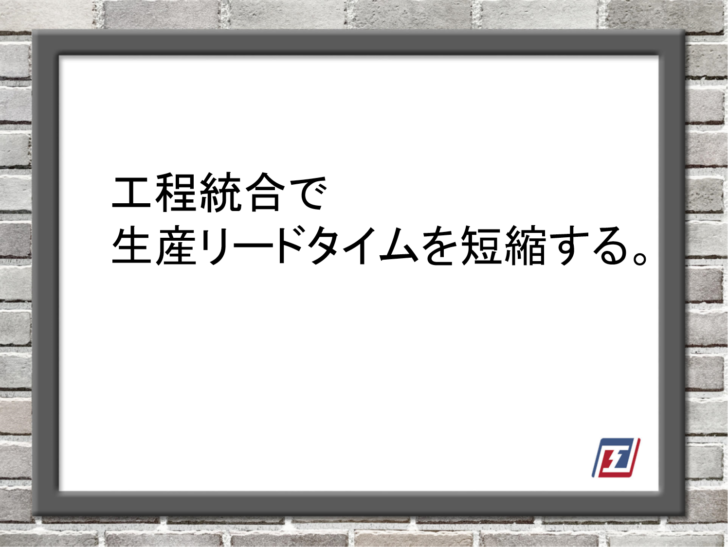
工程分割や工程統合の観点で現場を眺めたことはありますか?
1.工程分割
工程を分割すれば、一工程あたりの負荷は減ります。
どんどん分割していくと、
その工程で求められる作業は簡素化し、単純になるでしょう。
高い技能を持っていない作業者も短時間でその作業の専門家になれます。
組立て作業のような
労働集約的要素を含んだ工程の設計では、
しばしば、工程分割の考え方が取り入れられます。
困難は分割せよ。
自動車産業の黎明期、
フォードは、分業体制によって、
自動車の大量生産を実現させ、
安価な自動車を大衆へ行き渡らせました。
工程分割の本質は分業体制です。
その一方で、
工程分割には本質的なデメリットがあることも忘れてはなりません。
それは、新たなに「運搬」と「停滞」を生み出すことです。
工程分析4要素は
加工、運搬、停滞、検査ですが、
このうち、加工以外は、原則、価値を生みません。
工程を分割すると、価値を生まない作業が増えるのです。
では、工程を分割すると、なぜ、「運搬」と「停滞」が生み出されるのか?
仕掛品のためです。
ある特定の工程を想像して下さい。
その工程を分割してみます。
すると、前の工程と後ろの工程に
「つなぎ目」が必要になることが分かります。
その「つなぎ目」を埋めるモノが仕掛り品です。
仮に前後工程が完全に同期化していると、
理屈上、「つなぎ目」は不要となります。
が、製造条件の制約やバッファ機能などの理由で
「つなぎ目」を機能させなければならない現場がほとんどです。
仕掛品ゼロは
生産の流れをつくる上で究極の目標ですが、
現実的にはそうはなりません。
そして、その仕掛品が、
「圧倒的な納期」、超短納期の阻害要因となっています。
2.工程統合
リードタイム短縮でやるべきことは、
「停滞」「運搬」を除去し、スムーズな生産の流れをつくることです。
ですから、工程分割の逆となる、工程統合は、
リードタイム短縮の手段となります。
改善の着眼点ECRSの法則の2番目、
Cは合わせる(combain)ですが、
工程統合はまさにそれです。
製造ラインが工程順に並んだ
製品別レイアウトで、
設備が専用機であったりすると、
工程統合の改善を進める難易度は当然、高くなります。
したがって、
製品別レイアウトで専用機を並べる場合、
工程設計を慎重に進める必要があります。
一度設置した設備の変更はやりがたいですから。
一方、中小の多くの現場では、
機能毎にグループをつくる機能別レイアウトであることが多いです。
そうした場合、設備はほぼ汎用機になっています。
その現場の、
レイアウト変更に対する柔軟性は高いので、
あっちの設備をこっちへ移動し、
そちらの設備と並べる、
ということがある程度の労力できるのではないでしょうか?
こうした設備の並べ替えで、擬似的な工程統合ができます。
3.ある板金加工現場でのトライアル
板金加工ラインで実験的に工程統合をやってみたことがあります。
プレス工程→曲げ工程を対象にプレス機とベンダーを並べてみました。
プレス後、できあがった部品を
整理・確認、一旦保管、その後、
ベンダーの稼働に合わせて保管した部品を引っ張り出し、曲げ加工をしていました。
そこで、プレス機とベンダーを相互に寄せて並べます。
仕掛品がなくなり、作業の中抜きが可能となるのです。
プレス機とベンダーの稼働を同期させる工夫は
必要でしたが、
板材から一気に曲げ部品まで出来上がる状況は、
見ていて気持ちのいいものでした。
「モノの流れがすっきりしていいですね。」
現場リーダーの言葉です。
この試みは、
実戦までには至らなかったのですが、
十分にその効果を実感できました。
プレス機とベンダーの複合機を導入したわけでなく、
レイアウトを変更して、両者を並べただけです。
擬似的な工程統合ができました。
機会があれば、実戦へ向けて再挑戦です。
工程統合で生産性を高めるしくみを作りませんか?