戦略的工場経営ブログ多品種少量化を多品種化と少量化で分けて観る
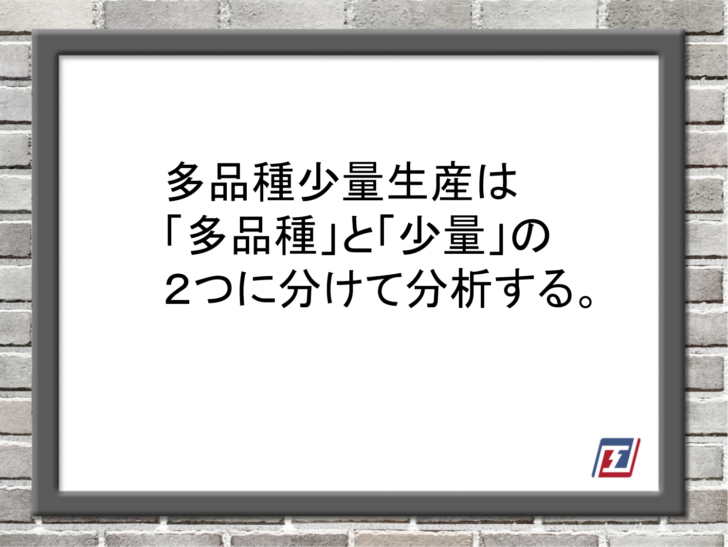
多品種生産、および小ロット生産の課題を把握していますか?
1.現場を通して感じた変化
25年以上製造業にかかわっていると、
現場をとおして、
いろいろな「変化」を感じることがあります。
皆さんの現場も、
仕事のやり方や設備をはじめとして、
現場の風景が5年前、10年前と全く同じということはないはずです。
技術者として現場で汗をかいていたころの話です。
「3年間、現場が変わっていなければ、それはエンジニアの怠慢だ。」
このように先輩技術者から常に発破をかけられていました。
今から25年以上も前のことです。
当時は”3年”でしたが、今なら、”1年”かもしれません。
技術高度化のスピードは年々速くなっています。
モノづくりの世界は技術で戦っています。
技術動向に目を配り、競合を出し抜く世界一水準の現場を、
維持してほしいという先輩技術者からのメッセージでした。
コア技術のブラシュアップ、
周辺技術の強化、
振り返れば、現場の生産技術、製造技術の変化を肌で感じてきたわけです。
また、作業環境を改善する目的で
自動化を進めた結果、
現場の風景が大きく変わったことも実感しています。
私たちは、モノづくりで
事業を展開しているわけですから、
現場における技術革新の停滞は、
市場からの退場を意味します。
コア技術やその周辺技術の深耕・強化は絶対です。
2.多品種少量化は多品種化と少量化
現場の風景を通して感じてきた技術面での変化の他に、じわじわ、変わっていたことがあります。
それは、現場で製品を管理する、言い換えると仕掛品や完成品を”追っかける”手間です。
90年代に比べて、00年代は、明らかに、手間が増えました。
つまり、「多品種少量化」です。
当時、勤務していた工場での多品種少量化の背景は2つありました。
・既存顧客の注文ロットが小さくなったこと。
・新規顧客を開拓したこと。
皆さんの工場でも、
背景はいろいろでしょうが、
結果として多品種少量化になっていることでしょう。
当時、所属していた工場の生産ラインは、世界トップクラスの生産性を誇っていました。
1980年代後半に稼働を開始し、平成バブル崩壊直前までの
旺盛な需要を取り込んで大いに収益を上げた生産ラインです。
前工程に複数台のプレスが設置され、
その後切削加工、塗装工程、梱包と流れて製品が完成する一貫ラインでした。
当時の生産形態は少品種多量生産です。
大量生産による効率向上で収益を確保していました。
生産ライン全体が、
前工程から後工程まで、1種類の製品で埋め尽くされることもしばしば。
その後、1990年代になり、
一時に流動する品種が3~4品種と増えていきました。
入社当時は、そんな状況でした。
そこから、多品種化が進み、
一時に流動する品種が7~8種類と増えていったのです。
多品種化が進むにつれて、
当然、管理すべき項目が増えます。
現場を管理する立場として、
特に目標品質(直行率、良品率)を管理するのに骨が折れました。
なにせ、多品種数分の品質に関する管理項目があるわけですから。
管理項目をフォローし、
フィードバックする負荷が、
従来より多くなることで、
多品種化を実感したものです。
その生産ラインは、例えるなら、
100個の製品を生産するとして(生産ラインの能力は一定なので)
A.1種類を100個
B.2種類を50個ずつ
C.10種類を10個ずつ
というように移行していったわけです。
ライン全体が、1種類の製品で埋め尽くされるようなときもしばしばだったというのはAの状態。
その当時を知る人が言っていました。
「数に圧倒はされたけど、管理自体はしやすかったね。」
数種類の製品で済むわけですから。
ひとつひとつの製品の管理を丁寧にできるのです。
従来にはない新たな管理項目を加え、
少々めんどうだなと思われる仕事でも現場はやってくれます。
ただし、これは、品種数がある程度限られている場合です。
ですから、多品種化の管理で留意しなければならないことがあります。
それは、「複雑にしない。簡素にする。」ということです。
そうでなくても、面倒を見なければならない品種数が多いわけです。
”いつもどおりに”、個別に、詳細な管理ポイントを提示しても、現場はやり切れません。
確実にやらせるため、個別には管理ポイントを絞らなければなりません。
ある時、
生産条件を整理した標準作業票が、あまりに複雑になり、
どの製品に、何を対応させればいいのか、
分かりにくいとの要望が現場から出たことがあります。
そこで、管理ポイントをシンプルにしました。
さらに、色分けする、図示するのように視覚的に一発で理解できる工夫もしました。
多品種で品種が増えたことに対する配慮が必要だったのです。
そして、
品種数が多いという要因の他に、
もうひとつ多品種化生産の難易度を上げている要因があります。
それは少量生産であること、言い換えると小ロットであるということです。
小ロットでは、品種切り替えの回数が増え、さらに、品種が切り替わる度に、
段取り替え作業の内容も変わります。
感覚的に理解できる人も多いと思いますが、
管理上、品質上のトラブルが起きやすいのは品種が切り替わったときです。
加えて、小ロット生産では作業自体の学習効果が得られにくいという側面もあります。
累積生産量が増えるにつれて、工数が減り生産性が高まるという経験則です。
少量生産はその効果が得られにくい状況にあります。
これまで、時間をかけて、何となく現場の頑張りに期待していた作業習熟度の向上を、
従来と同じように、期待することは難しくなります。
多品種生産の難易度が高いのは、生産ロットが小さいのも起因しているのです。
多品種少量化で直面する困りごとは、
下記の2つにわけ、どちら起因なのかを切り分けます。
・多品種化に起因すること
・少量化に起因すること
多品種少量化を多品種化と少量化の2つに分けて、問題の原因を探ります。
どちらにしても、管理ポイントを簡素にすることがカギです。
そういえば、改善手法である「ECRSの原則」にも簡素化が含まれていますね。
多品種生産、および小ロット生産で生産性を高める管理のやり方を考えませんか?