戦略的工場経営ブログトヨタのシングル段取りと仕組み化
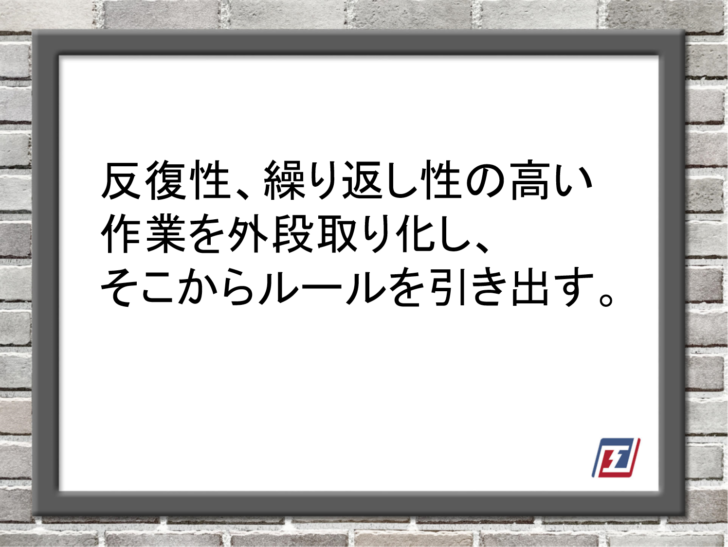
仕組み化とは単なるルール化にあらず。反復性、繰り返し性の高い作業を
外段取り化し、そこからルールを引き出す、という話です。
1.トヨタのシングル段取化の話
中小製造現場が目指すべき方向性のひとつはマスカスタマイゼーションです。
顧客の満足度を高める価値を届けます。
そして、これを実現させる生産形態は「1品1仕様の個別生産の連続ライン」です。
個別生産と連続ラインという二項対立の関係を両立させる必要があります。
カギは段取り時間の短縮です。
段取り時間短縮は次の2つの順番で考えます。
(1)内段取りを外段取りにできないか考える。
(2)内段取り時間を短縮できないか考える。
・ワンタッチ化
・治工具類、段取り作業場の確保
などが考えるポイントです。
トヨタ自動車における段取り時間短縮の話は有名です。
内段取りと外段取りに注目し、上記の(1)(2)をトコトンやりつくします。
その結果、2~3時間かかっていたプレスの段取り時間を3分にまで短縮させました。
このあたりの経緯をPHPオンライン衆知 2016年6月10日記事で紹介しています。
桑原晃弥著『トヨタ 最強の時間術』の記述を取り上げていました。
段取り替えには、
機械を止めて行う「内側の段取り(内段取り)」と、
機械の稼働中にも行える「外側の段取り(外段取り)」の
2つがあります。
これまで
内段取りだったものを外段取りにできれば、
段取り替え時間は大幅に短縮できるというアイデアでした。
これに従って改善を進めた結果、
段取り替えを
なんと1時間以内に短縮することができたのでした。
ところが大野氏(トヨタ自動車元副社長)は
満足せずとんでもない目標を設定します。
「3分間に短縮してくれ」と言うのです。
10分間を切る段取り替えを
特に「シングル段取り」といいますが、
一気にそこまで短縮しろという指示でした。
当時、西ドイツのフォルクスワーゲンでさえ
段取り替えには2時間を要していました。
1時間でも大変な記録といえます。
「それを、一気に3分間とは……とても不可能だ」と、
改善メンバーのほとんどが呆然としました。
でも、中には、
「トヨタ式の改善をさらに徹底すれば可能かもしれない」と
考える人もいました。
こうして再び改善が始まります。
内段取りを
さらにいくつも外段取りに追い込んだ上、
工具や金型をワンタッチで
取り換えられる工夫をこらしました。
締め具をボルトレスにしたり、
一回転締め具にするといった
細部までアイデアを出し、
100を越える改善を行ったといいます。
その結果、
ついに段取り替えは
本当に3分間でできるようになったのです。
これはトヨタ式にとっても大きなできごとでした。
時間はトヨタ式の最大の制約条件の一つでした。
ものづくりに求められるのは
生産スピードであり、量産化です。
トヨタ式の
「必要なものを、必要な時に、必要なだけ」
という要求は、
スピードおよび量産化と
長く二項対立の関係にありました。
それが、シングル段取りを実現したことで解決されたのです。
(出典:PHPオンライン衆知 2016年6月10日記事)
生産ラインは稼働させてなんぼのものです。
ですから、とにかく徹底的に止めないことにこだわります。
一方、
「必要なものを、必要な時に、必要なだけ」
という仕事では、
品種の「切り替え」が頻発します。
品種の「切り替え」作業、つまり段取り替え作業が増えます。
しかしながら、段取り替え作業が増えても生産性は維持しなければなりません。
そこで、1回当たりの段取り替え作業の時間を短縮する必要性に迫られたのです。
そこで、
・内段取りの外段取り化
・内段取りの時間短縮
という発想が生まれました。
一見、無理かもしれないテーマに直面しても、
できるかもしれない、
と考える現場メンバーが登場するあたりがトヨタらしいところです。
一朝一夕には、絶対に達成できない、
地道な仕事の積み重ねが、
後々の大きな成果につながったトヨタならではの象徴的な話です。
2.仕組み化は単なるルール化にあらず
トヨタは
・「必要なものを、必要な時に、必要なだけ」
・スピードおよび量産化
この2つの二項対立の関係をシングル段取りで両立させました。
複雑化していく業務を短時間でこなし、
すこしでも創造的な業務に
時間を割こうと考えるなら、
この段取時間短縮の考え方を適用するべきです。
業務の「仕組み化」。
これは、仕事の効率を上げる具体的な対応のひとつです。
カイゼンでいうところの歯止めです。
問題が発生した時、
対策を講じるわけですが、
継続性の可否が大切です。
その対策が、
対処療法に終わるか、
仕組みとなり歯止めとしての機能を果たすのかは、
この継続性で決まります。
継続性を重視する時、どこに着目するか?
それは、「反復性」の高い作業です。
「反復性」の高い作業に注目します。
そこを標準化し、実務上の負荷を減らすのです。
1)仕事を流れを整理
2)流れを構成している「作業」に分解
3)分解された「作業」を「反復性の高い」作業とそれ以外の作業に分類
4)「反復性の高い」作業を分析する。
5)「事前準備」できることを探る
反復性の高い作業を抽出し、
それらを集め、
一定のルールで処理することを考えます。
この「事前準備」は内段取りの外段取り化に相当します。
段取り時間の短縮と同様に、
これによって仕事の流れをスムーズにするのです。
例えば加工素材としての棒鋼を考えます。
この棒鋼を切断する工程から始まる生産ラインを想定します。
あらゆる製品はこの切断工程から開始されます。
ここに作業指示が集中します。
そして、生産指示は各製品ごとの担当者からバラバラになされているとします。
その結果、切断工程における他製品との調整業務は各担当者が負うことになります。
この調整業務は各製品担当にとって、時間がかかる負荷の高い「作業」です。
そこで、作業指示が重なった時の判断基準が決められていないと何が起きるでしょうか?
全体最適化の観点が抜けます。
早いもの勝ち。
職場での力関係。
こうしたことで日程が決まるのです。
顧客の都合よりも、自分たちの都合で日程が決まったりします。
判断基準が存在せず、現場丸投げ状態になっているからです。
こうした場合、
切断工程へ出される作業指示を全て集め、分類するのです。
反復性の高い太さ、長さの最大、最小を決定します。
頻繁に指示のある具体的な寸法を抽出します。
こうしたことが判明すれば、ルール化がやりやすくなるでしょう。
反復性の高い定番寸法の加工日程の枠を事前に決めることができます。
定番寸法は、自動的にそこへ組み込むルールにすればいいのです。
定番寸法への業務負荷は減ります。
減った業務負荷分だけ創造的な業務へ時間を廻すことができるのです。
この事例において、
5)項の「事前準備」にあたるのは、
「切断工程へ出される作業指示を全て集め、分類するのです。
反復性の高い太さ、長さの最大、最小を決定します。
頻繁に指示のある具体的な寸法を抽出します。」
この部分です。
反復性、繰り返し性の高い作業を外段取り化し、そこからルールを引き出すのです。
その業務に関係する全ての人の作業効率を上げられます。
3.「仕組み化」の目的は創造性の発揮
反復性、繰り返し性の高い作業を外段取り化し、
そこからルールを引き出す業務は
決して楽な仕事ではありません。
情報収集にも時間がかかります。
また、集めた情報をどう分類するべきなのか知恵を絞らねばなりません。
しかし、今後、「仕組み化」を現場で積極的に進める必要があります。
これからは、現場も創造性を発揮する時間を確保する必要に迫られるからです。
現場の全員が、
日々、あたふたと、
その日の「作業」に忙殺されている状況を放置しているとどうなるでしょうか?
この先、かなり厳しくなることを、
経営者は自覚する必要があります。
反復性、繰り返し性の高い作業を外段取り化し、そこからルールを引き出す仕組みをつくりませんか?